Mould of industrial filter base and using method thereof
A filter seat and mold technology, which is applied in the mold field of industrial filter seats, can solve the problems of air holes in the middle of the filter seat, and achieve the effect of reducing air holes and increasing density
- Summary
- Abstract
- Description
- Claims
- Application Information
AI Technical Summary
Problems solved by technology
Method used
Image
Examples
Embodiment Construction
[0016] The preferred embodiments of the present invention are given below in conjunction with the accompanying drawings to describe the technical solution of the present invention in detail.
[0017] Such as figure 1 and 2 As shown, the mold of the industrial filter seat of the present invention includes a body casting mold 6 for casting the filter seat body 1 , and a cavity is formed in the middle part of the body casting mold 6 . The body casting mold is a prior art and will not be described in detail here. The industrial filter holder mold of the present invention also includes a middle hole casting mold for casting the middle hole 11 passing through the filter holder body 1 on the filter holder body 1 .
[0018] The middle hole mold includes a pair of slider cores 2 that are separated from the opposite sides of the main body mold 6. The sum of the lengths of the two slider cores 2 is greater than or equal to the depth of the middle hole 11. The two slider cores 2 The di...
PUM
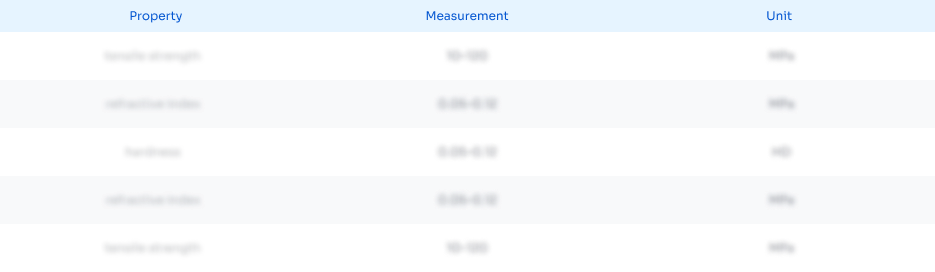
Abstract
Description
Claims
Application Information

- R&D
- Intellectual Property
- Life Sciences
- Materials
- Tech Scout
- Unparalleled Data Quality
- Higher Quality Content
- 60% Fewer Hallucinations
Browse by: Latest US Patents, China's latest patents, Technical Efficacy Thesaurus, Application Domain, Technology Topic, Popular Technical Reports.
© 2025 PatSnap. All rights reserved.Legal|Privacy policy|Modern Slavery Act Transparency Statement|Sitemap|About US| Contact US: help@patsnap.com