Work starting method for slurry bed Fisher-Tropsch synthesis
A technology of Fischer-Tropsch synthesis and slurry bed, which is applied in the preparation of liquid hydrocarbon mixtures and the petroleum industry. It can solve the problems of accelerated catalyst deactivation, increase of water pressure in the system, and unfavorable industrial operation, so as to improve stability and initial activity. The effect of high and low selectivity
- Summary
- Abstract
- Description
- Claims
- Application Information
AI Technical Summary
Problems solved by technology
Method used
Examples
example 1
[0021] Weigh an appropriate amount of reduced 20%Co0.8%Pt3%Zr / SiO 2 (Wt.) Fischer-Tropsch synthesis catalyst and paraffin, the volume ratio of catalyst to paraffin is 1:4, put into the slurry bed reactor, after airtight and gas replacement, the hydrogen mixed gas containing water vapor is introduced into the reactor And turn on the stirring device, the volume concentration of water vapor in the mixed gas is 2.5%, and the volumetric space velocity of the mixed gas is 1000h -1 , Raise temperature to 350℃, control pressure 3.5 MPa, after 2.5h, reduce temperature and pressure to 220℃, 2.0 MPa, switch H 2 / CO=2 (molar ratio) of synthesis gas for Fischer-Tropsch synthesis reaction. The reaction effluent is collected by a heat trap and a cold trap respectively. The catalyst conversion rate, methane selectivity and 200h stability test results are listed in Table 1.
example 2
[0023] Weigh an appropriate amount of reduced 20%Co1%Ni3%Zr / TiO 2 (Wt.) Fischer-Tropsch synthesis catalyst and paraffin, the volume ratio of catalyst to paraffin is 1:5, put into the slurry bed reactor, after airtight and gas replacement, the hydrogen mixed gas containing methanol vapor is passed into the reactor And turn on the stirring device, the volume concentration of water vapor in the mixed gas is 5%, and the volumetric space velocity of the mixed gas is 1500h -1 , Raise temperature to 300℃, control pressure 3MPa, after 1.5h, reduce temperature and pressure to 220℃, 2.0 MPa, switch H 2 / CO=2 (molar ratio) of synthesis gas for Fischer-Tropsch synthesis reaction. The reaction effluent is collected by a heat trap and a cold trap respectively. The catalyst conversion rate, methane selectivity and 200h stability test results are listed in Table 1.
example 3
[0025] Weigh an appropriate amount of reduced 20%Co0.05%Ru3%Zr / Al 2 O 3 (Wt.) Fischer-Tropsch synthesis catalyst and paraffin, the volume ratio of catalyst to paraffin is 1:5, put into the slurry bed reactor, after airtight and gas replacement, the hydrogen mixture containing acetone vapor is passed into the reactor And turn on the stirring device, the volume concentration of acetone vapor in the mixed gas is 2%, and the volumetric space velocity of the mixed gas is 800h -1 , Raise temperature to 250°C, control pressure 2.5MPa, after 1h, reduce temperature and pressure to 220°C, 2.0 MPa, switch H 2 / CO=2 (molar ratio) of synthesis gas for Fischer-Tropsch synthesis reaction. The reaction effluent is collected by a heat trap and a cold trap respectively. The catalyst conversion rate, methane selectivity and 200h stability test results are listed in Table 1.
[0026] Table 1 Reaction performance of the catalyst.
[0027] catalyst Initial activity and selectivity, CO conversion ra...
PUM
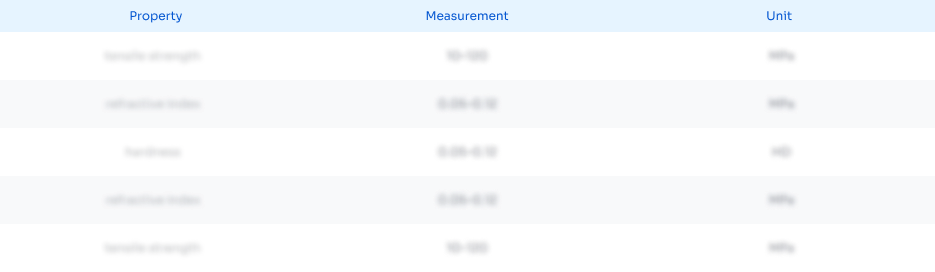
Abstract
Description
Claims
Application Information

- R&D
- Intellectual Property
- Life Sciences
- Materials
- Tech Scout
- Unparalleled Data Quality
- Higher Quality Content
- 60% Fewer Hallucinations
Browse by: Latest US Patents, China's latest patents, Technical Efficacy Thesaurus, Application Domain, Technology Topic, Popular Technical Reports.
© 2025 PatSnap. All rights reserved.Legal|Privacy policy|Modern Slavery Act Transparency Statement|Sitemap|About US| Contact US: help@patsnap.com