Preparation method of high-elasticity sole material
A shoe sole material and high elasticity technology, which is applied in the field of preparation of highly elastic shoe sole materials, can solve the problems of complex production process, high production cost, poor strength, etc., and achieve the effect of simple preparation process, low production cost and high wear resistance
- Summary
- Abstract
- Description
- Claims
- Application Information
AI Technical Summary
Problems solved by technology
Method used
Examples
Embodiment 1
[0007] A preparation method of a highly elastic shoe sole material, the preparation steps of the method are as follows: 60-66 parts by mass of xylene diisocyanate, 50-65 parts by mass of EVA, 10-12 parts by mass of rice bran, 30-35 parts by mass of polyether three Polyhydric alcohol, 3-6 parts by mass of talcum powder, 6 parts by mass of stearic acid, 13-15 parts by mass of stannous octoate, 2.5 parts by mass of thiosulfate and 3-3.5 parts by mass of naphthenic oil are added to the high-speed stirring mixer Mixing in the medium for 15 minutes; then adding to a twin-screw extruder to melt and graft for 4 hours to obtain the shoe sole material. The performance testing results of the sole material are as follows: relative density: 0.2, tensile strength / MPa: 2.8, rebound rate: 30%.
PUM
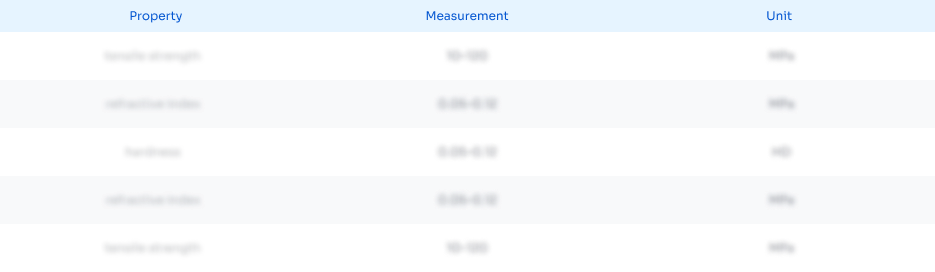
Abstract
Description
Claims
Application Information

- R&D Engineer
- R&D Manager
- IP Professional
- Industry Leading Data Capabilities
- Powerful AI technology
- Patent DNA Extraction
Browse by: Latest US Patents, China's latest patents, Technical Efficacy Thesaurus, Application Domain, Technology Topic.
© 2024 PatSnap. All rights reserved.Legal|Privacy policy|Modern Slavery Act Transparency Statement|Sitemap