Control device for motor drive system and vehicle having same
A technology of motor drive and control device, which is applied in the direction of controlling electromechanical transmission device, power consumption device, motor generator control, etc. to achieve the effect of improving efficiency
- Summary
- Abstract
- Description
- Claims
- Application Information
AI Technical Summary
Problems solved by technology
Method used
Image
Examples
Embodiment approach 1
[0101] In such a motor drive system, in order to increase the rotation speed or output of AC motor MG1 as described above, it is necessary to increase the system voltage VH. However, the system voltage VH cannot be set arbitrarily high, and is basically limited by the withstand voltage (withstand voltage) of devices such as converters and / or converters.
[0102] Figure 4 versus image 3 Similarly, it is a graph showing the relationship between the rotation speed MRN1 of the AC motor MG1 and the torque command value TR. in Figure 4 Here, the curve W2 shows the critical value at which the system voltage VH becomes the maximum value.
[0103] That is, the low speed side or low output side of the curve W2 is a region where the system voltage VH is variable. In this region, through the above-mentioned PWM control (sine wave PWM control and overmodulation PWM control), it is possible to control the motor to apply voltage. Size to get the desired speed and output torque. However, on t...
Embodiment approach 2
[0139] In the first embodiment, the following method is described: in the case of a low torque command, with respect to the maximum value Vdc of the system voltage VH, the boost command value is increased by easing the voltage variation caused by the control variation, so that The field weakening control area moves to the high-speed side to improve efficiency.
[0140] In the second embodiment, the following method is described. Furthermore, by considering the magnitude of the current flowing in the converter and the converter, the amount of voltage fluctuation due to the switching surge generated when the converter and the converter are switched is explained. , To increase the boost command value, thereby further improving efficiency.
[0141] Figure 13 versus Image 6 with Figure 7 It is also a diagram showing the withstand voltage of the inverter and the switching elements included in the converter. In the second embodiment, in addition to ΔV1 which is the amount of voltage f...
Embodiment approach 3
[0151] In the first and second embodiments, the following method is described: in the case of a low torque command, the maximum value Vdc of the system voltage VH is alleviated with respect to the amount of voltage fluctuation due to control fluctuations and switching surges, Increase the boost command value.
[0152] In the third embodiment, the following method will be described: especially when the torque command value is almost zero, the current flowing in the AC motor becomes very small, so that the switching operation is stopped and the system voltage VH is not performed. limits.
[0153] Figure 17 It is a diagram for explaining the outline content of Embodiment 3, which is similar to that in Embodiment 1 and Embodiment 2. Figure 7 with Figure 13 Similarly, a diagram showing the withstand voltage of the converter and the switching elements included in the converter.
[0154] Reference Figure 17 In the first and second embodiments, although the voltage fluctuation ΔV1 cause...
PUM
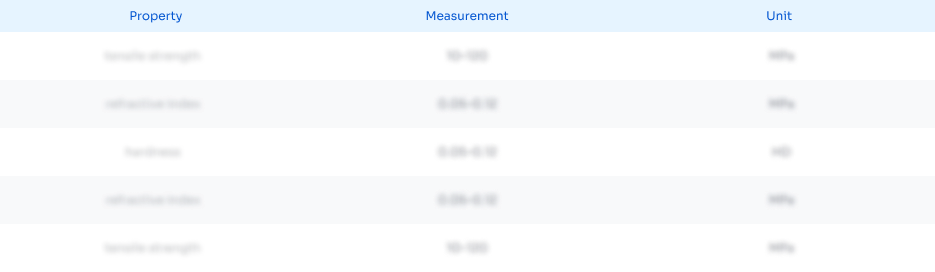
Abstract
Description
Claims
Application Information

- R&D
- Intellectual Property
- Life Sciences
- Materials
- Tech Scout
- Unparalleled Data Quality
- Higher Quality Content
- 60% Fewer Hallucinations
Browse by: Latest US Patents, China's latest patents, Technical Efficacy Thesaurus, Application Domain, Technology Topic, Popular Technical Reports.
© 2025 PatSnap. All rights reserved.Legal|Privacy policy|Modern Slavery Act Transparency Statement|Sitemap|About US| Contact US: help@patsnap.com