Maintenance method for converter lining
A converter lining and converter technology, applied in lining repair, manufacturing converters, etc., can solve problems such as increasing shutdown time, achieve the effects of protecting furnace lining, increasing viscosity, and improving converter operation rate
- Summary
- Abstract
- Description
- Claims
- Application Information
AI Technical Summary
Problems solved by technology
Method used
Examples
Embodiment 1
[0015] The 180-ton converter estimates that the total amount of slag is between 18 and 20 tons. During the process of tapping to the west side, the feeding material is manually added to the trunnion of the furnace lining, and the amount of magnesium feeding material added is controlled. At 80-150kg, at the same time, use a gunning gun to spray the gunning material on the furnace cap on the east side of the converter, and the spraying speed of the gunning gun is 60-100kg·min -1 , the amount of magnesia gunning material is generally controlled at 180kg-250kg, and the amount added is adjusted according to the actual slag state. After tapping, the slag splashing operation is directly performed to protect the furnace. The slag is not modified during the slag splashing process, and the slag can be removed within 3 minutes. Splash dry.
[0016] The average time of slag splashing in the original process is 4 minutes, and each shift needs to be shut down and sprayed for 10 minutes each...
Embodiment 2
[0018] The total amount of slag in the 180-ton converter is estimated to be between 15 and 17 tons according to the smelting conditions. During the process of tapping to the west side of the 180-ton converter, the feeding material is manually fed to the trunnion of the furnace lining. The magnesium feeding material is The amount of slag is generally controlled at 150kg to 250kg, and the amount added is adjusted according to the actual slag state. After the steel is tapped, the slag splashing operation is performed directly to protect the furnace. The slag is not modified during the slag splashing process, and the slag can be splashed dry within 2.5 minutes.
[0019] The average time of slag splashing in the original process is 4 minutes, and each shift needs to be shut down and sprayed for 10 minutes each time. After adopting this process, the slag splashing time can be shortened by 1.5 minutes, and the converter does not need to be shut down for spraying. The average daily outp...
Embodiment 3
[0021] The total amount of slag in a 180-ton converter is estimated to be between 17 and 19 tons. After shaking the furnace to the east to measure the temperature and take samples, and within 5 minutes of waiting for the test results, use a gunning gun to spray the gunning material on the furnace on the west side of the converter. For the cap part, the spraying speed of the gunning gun is 60-100kg·min -1 , the amount of magnesium gunning material is generally controlled at 300-450kg, adjust the amount according to the actual slag state, and then shake to the west side for tapping operation, after the steel tapping is completed, directly carry out the slag splashing operation to protect the furnace, and the slag splashing process is not carried out The slag is modified, and the slag can be splashed dry within 3.5 minutes.
[0022] The average time of slag splashing in the original process is 4 minutes, and each shift needs to be stopped for 10 minutes for gunning. After adoptin...
PUM
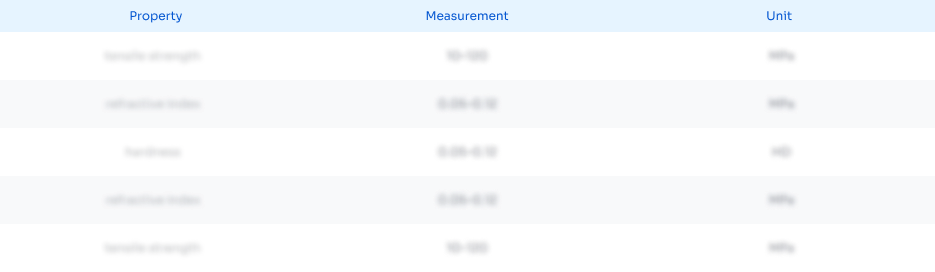
Abstract
Description
Claims
Application Information

- R&D
- Intellectual Property
- Life Sciences
- Materials
- Tech Scout
- Unparalleled Data Quality
- Higher Quality Content
- 60% Fewer Hallucinations
Browse by: Latest US Patents, China's latest patents, Technical Efficacy Thesaurus, Application Domain, Technology Topic, Popular Technical Reports.
© 2025 PatSnap. All rights reserved.Legal|Privacy policy|Modern Slavery Act Transparency Statement|Sitemap|About US| Contact US: help@patsnap.com