Method for measuring container position and state on basis of structured light visual sensor
A visual sensor and container technology, applied in the field of camera measurement and mechanical automation, can solve the problems of high technical and experience requirements of operators, high operation difficulty and low operation efficiency.
- Summary
- Abstract
- Description
- Claims
- Application Information
AI Technical Summary
Problems solved by technology
Method used
Image
Examples
Embodiment Construction
[0034] Such as figure 1 Based on the structured light vision sensor, the container position and attitude measurement system is realized. The structured light vision sensor installed on the container handling equipment and capable of sensitive container edge and / or corner hole information projects structured light to the container surface and takes images, and obtains the container by processing the image. Structural features such as edges, corner holes and / or vertices, use the features to calculate the position and attitude relationship of the container relative to the spreader, the structured light vision sensor is composed of a camera, a structured light projector, a data processor, etc., and the camera is used to project Container imaging with structured light, the data processor is used for image analysis and coordinate calculation.
[0035] Such as figure 2 , after the structured light vision sensor and the spreader are fixed, the relative position and posture relations...
PUM
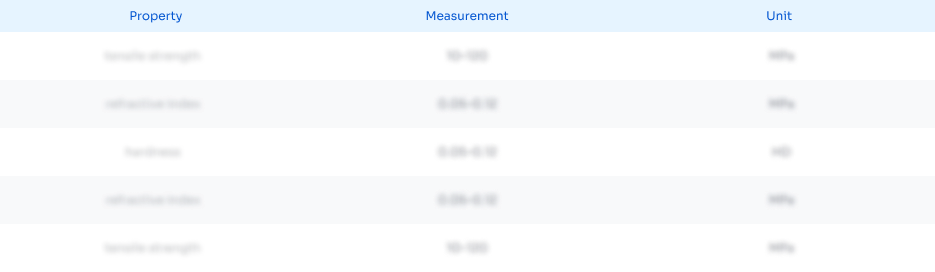
Abstract
Description
Claims
Application Information

- Generate Ideas
- Intellectual Property
- Life Sciences
- Materials
- Tech Scout
- Unparalleled Data Quality
- Higher Quality Content
- 60% Fewer Hallucinations
Browse by: Latest US Patents, China's latest patents, Technical Efficacy Thesaurus, Application Domain, Technology Topic, Popular Technical Reports.
© 2025 PatSnap. All rights reserved.Legal|Privacy policy|Modern Slavery Act Transparency Statement|Sitemap|About US| Contact US: help@patsnap.com