Input-output complete decoupling three-freedom-degree moving parallel robot mechanism
A completely decoupled, degree-of-freedom technology, applied in the field of robotics, can solve the problems of small working space of parallel robot mechanism, limited control algorithm application, complex dynamic model, etc., to achieve the effect of easy trajectory planning, simple structure and low manufacturing cost
- Summary
- Abstract
- Description
- Claims
- Application Information
AI Technical Summary
Problems solved by technology
Method used
Image
Examples
Embodiment Construction
[0011] exist figure 1 A schematic diagram of the structure of a three-degree-of-freedom mobile parallel robot mechanism with fully decoupled input-output is shown. It consists of two connecting rods, wherein one end of a connecting rod 3 of the first branch is connected to the fixed platform 1 through the moving pair 2, and one end of the other connecting rod 5 is connected to the moving platform 7 through the moving pair 6. The above two connecting rods The other end is connected through mobile pair 4. One end of a connecting rod 11 of the second branch links to each other with the fixed platform through the moving pair 13, and one end of the other connecting rod 10 links to each other with the moving platform through the moving pair 9, and the other ends of the above-mentioned two connecting rods link through the moving pair 12. The normal directions of the moving pairs 2 and 12 in the above two branches are parallel to each other, the normal directions of the moving pairs ...
PUM
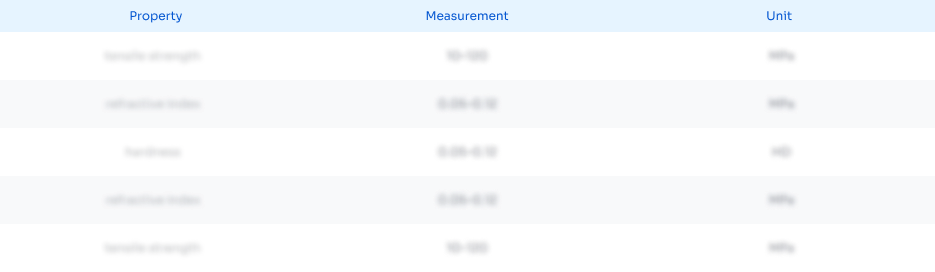
Abstract
Description
Claims
Application Information

- R&D Engineer
- R&D Manager
- IP Professional
- Industry Leading Data Capabilities
- Powerful AI technology
- Patent DNA Extraction
Browse by: Latest US Patents, China's latest patents, Technical Efficacy Thesaurus, Application Domain, Technology Topic, Popular Technical Reports.
© 2024 PatSnap. All rights reserved.Legal|Privacy policy|Modern Slavery Act Transparency Statement|Sitemap|About US| Contact US: help@patsnap.com