Machining method of high-accuracy cutter shaft of rotary shear
A processing method and disc shearing technology, applied in metal processing equipment, manufacturing tools, machine tools suitable for grinding workpiece planes, etc., can solve the unstable processing of product end face runout, the difficulty in evaluating the percentage of meshing surface, and the disadvantageous Produce high-precision products and other issues to ensure the coaxiality of products, avoid processing instability, and improve benchmark stability
- Summary
- Abstract
- Description
- Claims
- Application Information
AI Technical Summary
Problems solved by technology
Method used
Image
Examples
Embodiment Construction
[0042] refer to image 3 , the axial end face grinding method of the shaft shoulder of the present invention, the shaft 100 is provided with a shaft shoulder 101, and a groove 201 is provided in the middle of the axial end face of the grinding wheel 200, the groove on the grinding wheel is an annular groove, and the grinding wheel 200 The vertical distance H between the peripheral surface and the inner annular surface of the groove 201 is greater than or equal to 1.5 times the height of the shoulder 101 . The distance L between the groove on the grinding wheel and the axial end surface of the grinding part is 1-2 mm. The part that is clamped between the groove 201 and the peripheral surface of the grinding wheel is the grinding part 202 of the grinding wheel, so that the grinding part of the grinding wheel in the rotating process is clamped on the machine tool and is in the end surface of the shaft shoulder in the rotating process. Grinding: During the grinding process, the g...
PUM
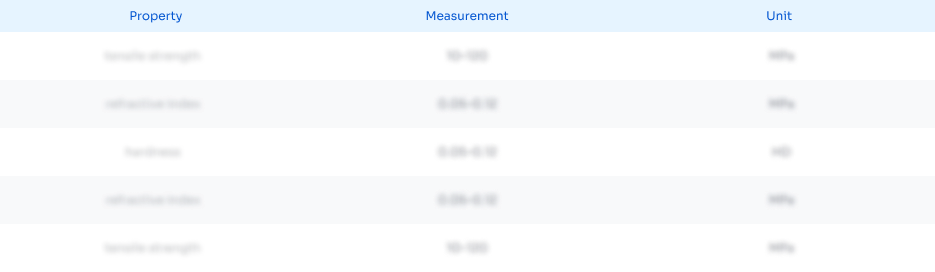
Abstract
Description
Claims
Application Information

- R&D Engineer
- R&D Manager
- IP Professional
- Industry Leading Data Capabilities
- Powerful AI technology
- Patent DNA Extraction
Browse by: Latest US Patents, China's latest patents, Technical Efficacy Thesaurus, Application Domain, Technology Topic, Popular Technical Reports.
© 2024 PatSnap. All rights reserved.Legal|Privacy policy|Modern Slavery Act Transparency Statement|Sitemap|About US| Contact US: help@patsnap.com