Large-size end surface processing electric spindle for mixed support of hydrostatic bearing and rolling bearing
A technology of hydrostatic sliding bearings and rolling bearings, which is applied to metal processing equipment, manufacturing tools, and parts of grinding machine tools. The effect of extending the service life
- Summary
- Abstract
- Description
- Claims
- Application Information
AI Technical Summary
Problems solved by technology
Method used
Image
Examples
Embodiment Construction
[0016] The electric spindle supported by the hydrostatic sliding bearing and the rolling bearing of the present invention is as follows: figure 1 As shown, it mainly includes: rotating shaft 6, rotor sleeve 23, motor rotor 22, motor stator 21, cooling water jacket 20, double row cylindrical roller bearing 25, squeeze oil film damper 27, self-aligning ball bearing 18, static The closed static pressure thrust bearing that pressure thrust bearing 9 and 10 forms, thrust plate 16, rotor 14, motor housing 7 etc. The rotating shaft 6 is a stepped shaft, the rotor sleeve 23 is installed in the middle of the rotating shaft 6, the motor rotor 22 is installed on the rotor sleeve 23, the cooling water jacket 20 and the motor stator 21 are installed in the motor casing 7, and the motor casing 7 is provided with a motor Cooling water inlet 5 and cooling water outlet 19. The upper casing 4 is installed on the upper end of the motor casing 7 and connected with the motor casing 7 by several ...
PUM
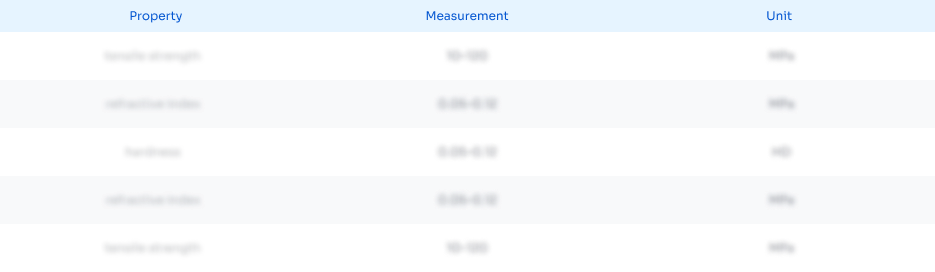
Abstract
Description
Claims
Application Information

- R&D Engineer
- R&D Manager
- IP Professional
- Industry Leading Data Capabilities
- Powerful AI technology
- Patent DNA Extraction
Browse by: Latest US Patents, China's latest patents, Technical Efficacy Thesaurus, Application Domain, Technology Topic, Popular Technical Reports.
© 2024 PatSnap. All rights reserved.Legal|Privacy policy|Modern Slavery Act Transparency Statement|Sitemap|About US| Contact US: help@patsnap.com