A simple-supported and then continuous prefabricated monolithic composite continuous bridge and its construction method
A simply supported and then continuous, prefabricated girder technology, which is applied in bridges, bridge construction, erection/assembly of bridges, etc., can solve the problems of poor connection integrity of prefabricated bridges, slow manufacturing and installation speed, and high formwork amortization cost, etc., to achieve formwork The effect of low amortization cost, good beam synergy performance and convenient construction
- Summary
- Abstract
- Description
- Claims
- Application Information
AI Technical Summary
Problems solved by technology
Method used
Image
Examples
Embodiment Construction
[0044] see Figure 1 to Figure 10 , an embodiment of a simple-supported and then continuous prefabricated monolithic laminated continuous bridge provided in the present invention includes an inverted T-shaped prestressed prefabricated beam part 1, a cast-in-place part 2 and a diaphragm 3. The pouring part 2 includes a cast-in-place slab 21 and a cast-in-place superimposed part 22 on the upper part of the beam. The lower flange 11 of the inverted T-shaped prestressed prefabricated beam 1 and the upper part of the web 12 are embedded with pre-tensioned prestressed steel strands 4. The transverse diaphragm 3 is a prefabricated plate, and the transverse diaphragm 3 is arranged between the webs 12 of adjacent inverted T-shaped prestressed prefabricated beams at a certain distance along the longitudinal direction, and is located above the lower flange 11 of the prefabricated beam 1 . In the present invention, a superimposed continuous bridge is formed by the prefabricated beam 1, t...
PUM
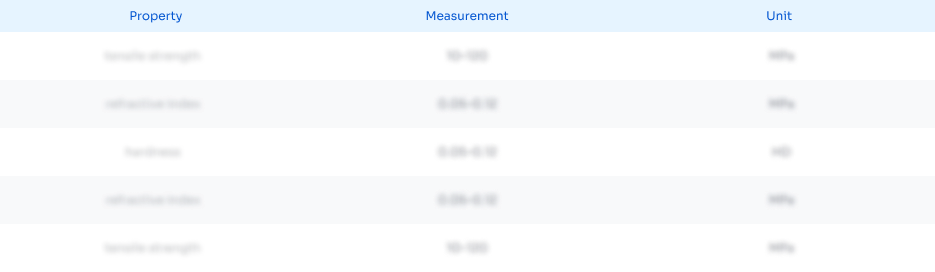
Abstract
Description
Claims
Application Information

- R&D
- Intellectual Property
- Life Sciences
- Materials
- Tech Scout
- Unparalleled Data Quality
- Higher Quality Content
- 60% Fewer Hallucinations
Browse by: Latest US Patents, China's latest patents, Technical Efficacy Thesaurus, Application Domain, Technology Topic, Popular Technical Reports.
© 2025 PatSnap. All rights reserved.Legal|Privacy policy|Modern Slavery Act Transparency Statement|Sitemap|About US| Contact US: help@patsnap.com