Method for preparing compound conductive layer on surface of epoxy resin
A composite conductive layer and epoxy resin technology, applied in the plating, coating, metal material coating process of superimposed layers, etc., can solve the problems of low heat resistance and poor aging resistance of polyethylene, and achieve excellent performance. , smoothness enhancement, the effect of enhancing conductivity
- Summary
- Abstract
- Description
- Claims
- Application Information
AI Technical Summary
Problems solved by technology
Method used
Examples
Embodiment Construction
[0017] The steps of the method of the present invention are as follows:
[0018] (1) Stress removal: The presence of stress on the specimen will affect the bonding force between the substrate and the coating. The stress detection method of plastic parts adopts the acetic acid immersion method, that is, the specimen is completely immersed in glacial acetic acid at about 24°C for 30 seconds, and immediately after taking it out Clean and dry, check the surface of the test piece; carefully check the appearance, if a small and dense crack is found somewhere, it means that there is stress in the test piece at this place; in the present invention, the epoxy resin is mixed in an acetone aqueous solution with a volume ratio of 25%. Soak for 30 minutes to remove the surface stress of the specimen;
[0019] (2), degreasing: the formula of degreasing agent is sodium carbonate 10-20g / L, sodium phosphate 10-20g / L, sodium silicate 10-20g / L, 2-3g / L emulsifier OP-10, Use a degreasing agent to...
PUM
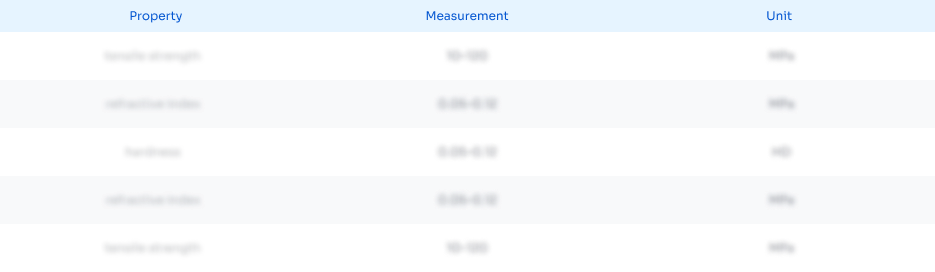
Abstract
Description
Claims
Application Information

- R&D
- Intellectual Property
- Life Sciences
- Materials
- Tech Scout
- Unparalleled Data Quality
- Higher Quality Content
- 60% Fewer Hallucinations
Browse by: Latest US Patents, China's latest patents, Technical Efficacy Thesaurus, Application Domain, Technology Topic, Popular Technical Reports.
© 2025 PatSnap. All rights reserved.Legal|Privacy policy|Modern Slavery Act Transparency Statement|Sitemap|About US| Contact US: help@patsnap.com