Method for manufacturing yellow disperse dyes
A manufacturing method and technology of disperse dyes, which can be used in dyeing, textiles, papermaking, ketones, etc., can solve expensive and uneconomical problems, and achieve the effect of industrial production and excellent light fastness
- Summary
- Abstract
- Description
- Claims
- Application Information
AI Technical Summary
Problems solved by technology
Method used
Image
Examples
Embodiment 1
[0069] Add 50 parts of 4-methoxy-2-nitroaniline to 131 parts of acetic acid at room temperature while stirring, and add 36 parts of acetic anhydride dropwise while stirring. After heating to 35°C, stir at 35~40°C 1 hour. After the reaction, 400 parts of water was added while stirring for crystallization. The crystals were filtered, washed with water, and dried to obtain 57.5 parts of A body (R is an acetyl group). Next, 61.1 parts of iron powder and 8.2 parts of acetic acid were added to 56.6 parts of dimethylformamide and 60 parts of water, heated to 85°C, and stirred at 85 to 90°C for 1 hour. All the obtained body A was dissolved in 169.9 parts of dimethylformamide, and then the solution was added dropwise over 1 hour and reacted at 85 to 90°C for 30 minutes. After the reaction, the iron powder was filtered out immediately, and the remaining reaction liquid was washed out from the iron powder with 56.6 parts of dimethylformamide. The obtained reaction solution containing B...
Embodiment 2
[0071] Add 34 parts of 4-methoxy-2-nitroaniline to 100 parts of acetic acid at room temperature while stirring. Add 30 parts of acetic anhydride dropwise with stirring at 0-40℃, and stir at 20-40℃ for 1 hour. After the reaction, 500 parts of water was added while stirring for crystallization. The crystal was filtered, washed with water, and dried to obtain 38.6 parts of A body (R is an acetyl group). Next, 16 parts of iron powder and 2.8 parts of acetic acid were added to 111 parts of isopropanol and 40 parts of water, heated to 85°C, and stirred at 85 to 90°C for 1 hour. Using 100 parts of isopropanol, 20 parts of the obtained body A was made into a slurry, and then the slurry was dropped over 1 hour, and reacted at 85 to 90°C for 30 minutes. After the reaction, the iron powder was filtered out immediately, and the remaining reaction liquid was washed out from the iron powder with 50 parts of isopropanol. The obtained reaction solution containing B body (R is an acetyl grou...
Embodiment 3
[0073] To 103 parts of the solution (approximately 300 parts) obtained by combining the B-body (R is an acetyl group)-containing reaction solution and the washing liquid obtained in the same manner as in Example 2, 5.2 parts of piperidine and 7.1 parts were added while stirring. 1,8-Naphthalenedicarboxylic acid anhydride, and it took 1 hour to heat to 83°C. After reacting at 81~83°C for 12 hours, it was naturally cooled to 35°C. Then, 500 parts of water was added while stirring for crystallization. The crystals were filtered and washed with water to obtain 35.3 parts of a wet cake of body C (R is an acetyl group). Next, 6.8 parts of the obtained C body was added to 49 parts of isopropanol while stirring, and 49 parts of water and 19.6 parts of 35% hydrochloric acid were added, and the mixture was heated to 82°C. React under reflux at 82°C for 10 hours, and cool to room temperature naturally. Add about 45 parts of 25% sodium hydroxide aqueous solution, adjust the pH to 8-9, a...
PUM
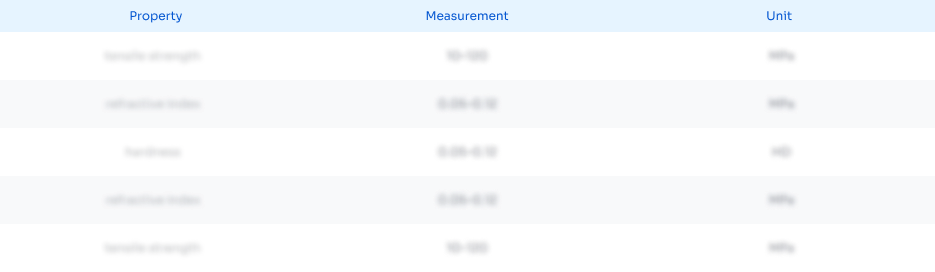
Abstract
Description
Claims
Application Information

- R&D
- Intellectual Property
- Life Sciences
- Materials
- Tech Scout
- Unparalleled Data Quality
- Higher Quality Content
- 60% Fewer Hallucinations
Browse by: Latest US Patents, China's latest patents, Technical Efficacy Thesaurus, Application Domain, Technology Topic, Popular Technical Reports.
© 2025 PatSnap. All rights reserved.Legal|Privacy policy|Modern Slavery Act Transparency Statement|Sitemap|About US| Contact US: help@patsnap.com