Method for preparing sulphoaluminate cement by using fluorine-containing sludge
A technology for sulfoaluminate cement and sludge is applied in the field of environmental engineering, which can solve the problems of waste of resources and occupation of landfill resources, and achieve the effect of saving energy and protecting the environment.
- Summary
- Abstract
- Description
- Claims
- Application Information
AI Technical Summary
Problems solved by technology
Method used
Examples
Embodiment 1
[0012] Embodiment 1: (1) solidification and drying of fluorine-containing sludge, the sludge with higher fluorine content obtained in the sewage plant, adding curing agent and stabilizer to the sludge, and then by mechanical stirring, the sludge and The curing stabilizer is mixed well. A solidified fluorine-containing sludge is obtained. (2) Production of sulphoaluminate cement; 1) Preparation of raw meal. The raw materials used in sulphoaluminate cement are limestone, bauxite and gypsum. The specific ratio is: limestone 45%, Al2O3 25%, SiO2 15%, gypsum 12%, fluorine-containing sludge 3%; 2) Clinker firing, raw meal is generally calcined in a rotary kiln at a temperature of 1300-1400°C The clinker formation process is as follows: at 950°C, C4A3S and C2AS begin to form; at 1100°C, C2S appears; at 1200°C, C2AS disappears, and 2C2S·CaSO appears 4 ; At 1250°C, C2S increases; at 1300-1400°C, 2C2S·CaSO 4 Disappeared, the clinker burned. 3) Cement preparation, sulphoaluminate cem...
Embodiment 2
[0013] Example 2: (1) solidification and drying of fluorine-containing sludge, the sludge with a larger fluorine content obtained in a sewage plant is added to the sludge with a solidifying agent and a stabilizer, and then by mechanical stirring, the sludge and The curing stabilizer is mixed well. Obtain solidified sludge. (2) Production of sulphoaluminate cement, 1) Preparation of raw meal. The raw materials used in sulphoaluminate cement are limestone, bauxite and gypsum. The specific ratio is: limestone 50%, Al2O3 25%, SiO2 10%, gypsum 14%, fluorine-containing sludge 1%; 2) Clinker firing, raw meal is generally calcined in a rotary kiln at a temperature of 1300-1400 °C After calcination, the clinker formation process is: at 950°C, C4A3S and C2AS begin to form; at 1100°C, C2S appears; at 1200°C, C2AS disappears, and 2C2S·CaSO appears 4 ; At 1250°C, C2S increases; at 1300-1400°C, 2C2S·CaSO 4 Disappears, and the clinker burns. 3) Cement preparation, sulphoaluminate cement,...
PUM
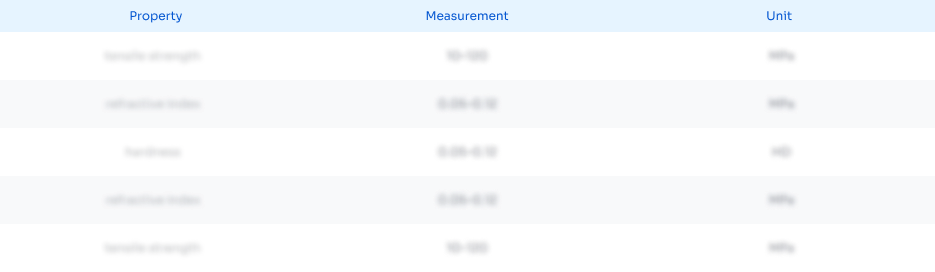
Abstract
Description
Claims
Application Information

- R&D
- Intellectual Property
- Life Sciences
- Materials
- Tech Scout
- Unparalleled Data Quality
- Higher Quality Content
- 60% Fewer Hallucinations
Browse by: Latest US Patents, China's latest patents, Technical Efficacy Thesaurus, Application Domain, Technology Topic, Popular Technical Reports.
© 2025 PatSnap. All rights reserved.Legal|Privacy policy|Modern Slavery Act Transparency Statement|Sitemap|About US| Contact US: help@patsnap.com