Dry quenched waste gas generating and coke modifying device
A technology of coke upgrading and dry quenching, applied in coke ovens, coke cooling, energy input, etc., can solve the problems of low production efficiency, inability to carry out continuous production, no waste gas export, recovery and purification and utilization, etc., to reduce coke making cost effect
- Summary
- Abstract
- Description
- Claims
- Application Information
AI Technical Summary
Problems solved by technology
Method used
Image
Examples
Embodiment Construction
[0026] The specific embodiments of the CDQ waste gas generation and coke upgrading device of the present invention are mainly introduced in detail in Section 3 of Chapter 1 of Part V and Sections 1, 2, 3 and 4 of Part 4 below.
[0027] Part 1 Furnace Coal Proportion and Preparation
[0028] If 5 different coals are selected, they are respectively gas coal, fat coal, coking coal, one-third coking coal, and lean coal, which are first mixed and then sieved and crushed until the broken particles reach below 5mm to form the furnace coal. Of course, the coal of the present invention is heated The decomposing furnace is equally applicable to other proportions and particle sizes of the furnace-feeding coal, and does not constitute a limitation to the furnace-feeding coal powder required by the coal pyrolysis furnace of the present invention.
[0029] Part 2 Dehydration of incoming coal
[0030] The incoming coal entering the coal pyrolysis furnace is dehydrated in advance through the...
PUM
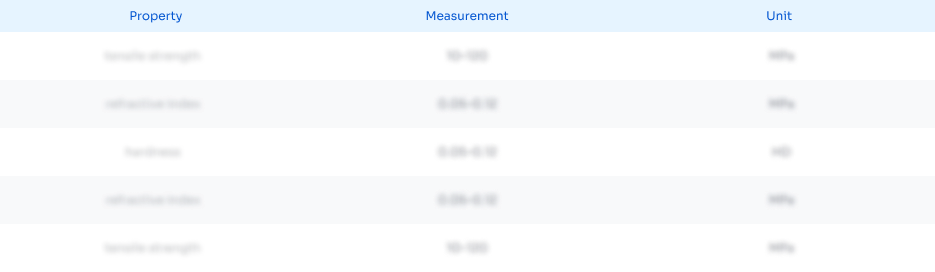
Abstract
Description
Claims
Application Information

- R&D
- Intellectual Property
- Life Sciences
- Materials
- Tech Scout
- Unparalleled Data Quality
- Higher Quality Content
- 60% Fewer Hallucinations
Browse by: Latest US Patents, China's latest patents, Technical Efficacy Thesaurus, Application Domain, Technology Topic, Popular Technical Reports.
© 2025 PatSnap. All rights reserved.Legal|Privacy policy|Modern Slavery Act Transparency Statement|Sitemap|About US| Contact US: help@patsnap.com