Differential capacitive micro-acceleration transducer and manufacturing method thereof
A technology of micro-acceleration and differential capacitance, which is applied in the direction of measurement of acceleration, velocity/acceleration/shock measurement, piezoelectric device/electrostrictive device, etc. It can solve the problems of complex test methods, avoid repeated photolithography, small stiffness, The effect of improving sensitivity
- Summary
- Abstract
- Description
- Claims
- Application Information
AI Technical Summary
Problems solved by technology
Method used
Image
Examples
Embodiment 1
[0074] Such as Figures 1a to 1i As mentioned above, this embodiment provides a method for manufacturing a differential capacitive micro-acceleration sensor, comprising the following steps:
[0075] Step S1: if Figure 1a As shown, a glass substrate 1 is provided, and a metal layer 2 is evaporated or deposited on the front side of the glass substrate 1 by electron beams. The material of the metal layer 2 is tentatively selected as Au, but it is not limited thereto. In other In the embodiment, it can also be a conductive metal such as Al, Cu, or Ag; then, a pair of interdigitated fixed electrodes 20 and two fixed electrode contacts 21 are produced by performing photolithography and etching on the metal layer 2 .
[0076] Step S2: Provide a structural substrate 3. In this embodiment, the structural substrate is temporarily selected as a silicon wafer, but it is not limited thereto. In other embodiments, it can also be other substrates, and different structural substrate process...
Embodiment 2
[0088] As shown in Figures 2a to 2e, they are part of the process flow chart for making a differential capacitive micro-acceleration sensor in this embodiment. This embodiment provides another method for manufacturing a differential capacitive micro-acceleration sensor, which is different from the first embodiment. The substrate provided in this embodiment is a silicon substrate, therefore, the difference in the substrate leads to a slight difference in the process, and the specific process steps are as follows:
[0089] When a silicon substrate 1 is provided, step S1 of the first embodiment further includes:
[0090] S1-1: If Figure 2a As shown, a substrate 1 is provided, and a silicon oxide layer 9 is thermally oxidized and grown on the front side of the silicon substrate, and the silicon oxide layer 9 insulates the silicon substrate from the metal layer 2 in subsequent steps.
[0091] S1-2: If Figure 2b As shown, a layer of metal layer 2 is prepared on the silicon oxide...
Embodiment 3
[0098] As shown in Figures 3a to 3d, it is a partial process flow chart of making a differential capacitive micro-acceleration sensor in this embodiment. This embodiment provides another method for manufacturing a differential capacitive micro-acceleration sensor, which is different from the first embodiment. The structural substrate provided in this embodiment is an SOI substrate. Therefore, the difference in the structural substrate also leads to a slight difference in the process. The specific process steps are as follows:
[0099] When providing an SOI structure substrate 3, step S2 of the first embodiment further includes:
[0100] S2-1: If Figure 3a As shown, a structural substrate 3 is provided, and a layer of silicon oxide 9 is thermally oxidized and grown on the surface of the top layer silicon 36 on the back of the structural substrate 3 .
[0101] S2-2: If Figure 3b As shown, photolithography and etching are carried out on the silicon oxide layer 9 on the back s...
PUM
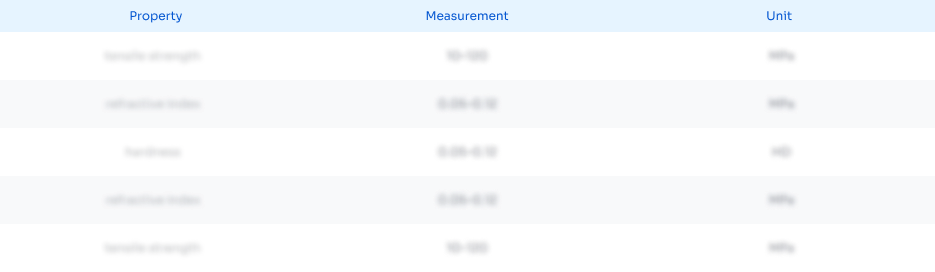
Abstract
Description
Claims
Application Information

- Generate Ideas
- Intellectual Property
- Life Sciences
- Materials
- Tech Scout
- Unparalleled Data Quality
- Higher Quality Content
- 60% Fewer Hallucinations
Browse by: Latest US Patents, China's latest patents, Technical Efficacy Thesaurus, Application Domain, Technology Topic, Popular Technical Reports.
© 2025 PatSnap. All rights reserved.Legal|Privacy policy|Modern Slavery Act Transparency Statement|Sitemap|About US| Contact US: help@patsnap.com