Backflow-preventing pipe joint
A technology of pipe joints and heads, which is applied in the field of pipe joints, can solve the problems of limited installation space of pipe joints, and achieve the effects of simple structure, easy production and processing, and convenient installation
- Summary
- Abstract
- Description
- Claims
- Application Information
AI Technical Summary
Problems solved by technology
Method used
Image
Examples
Embodiment 1
[0018] Such as figure 1 , figure 2 As shown, the pipe joint capable of preventing backflow of the present invention is a two-way joint in this embodiment, including a joint body 1, and the joint body 1 is provided with an inlet port 11 and an outlet port 12, and the inlet port 11 and the outlet port 12 A channel A through the joint body 1 is formed between them,
[0019] A spool 2 that can be limitedly moved along the channel A is provided in one of the channels A, and the spool 2 includes a head 21 facing the inlet end 11 and a tail 22 facing the outlet end 12;
[0020] A snap ring 3 is arranged behind the tail portion 22 of the spool 2 in the passage A, and a spring 4 is tightly pressed between the tail portion 22 of the spool 2 and the snap ring 3;
[0021] The head 21 of the valve core 2 has a conical outer wall 21a, and the inside of the valve core 2 has a flow hole 23 communicating with its conical outer wall 21a and the tail portion 22. The cross section of the flow ...
Embodiment 2
[0025] Such as Figure 3 ~ Figure 4 Shown is the second embodiment of the present invention, which differs from the first embodiment in that: in this embodiment, the pipe joint is a three-way joint, that is, the joint body 1 is provided with two outlet ports 12, Two passages A, B are formed between the inlet port 11 and the two outlet ports 12, and the valve core 2 is arranged in one of the passages A.
PUM
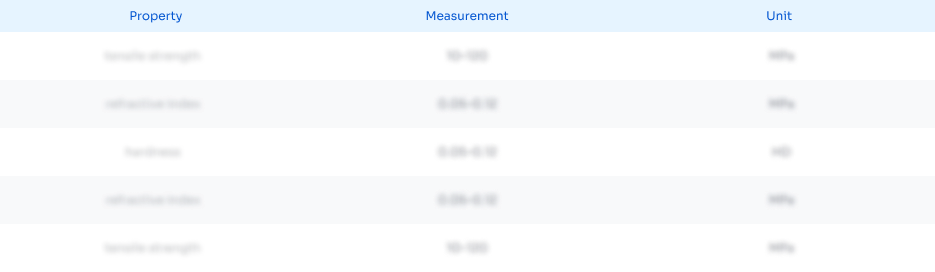
Abstract
Description
Claims
Application Information

- R&D Engineer
- R&D Manager
- IP Professional
- Industry Leading Data Capabilities
- Powerful AI technology
- Patent DNA Extraction
Browse by: Latest US Patents, China's latest patents, Technical Efficacy Thesaurus, Application Domain, Technology Topic, Popular Technical Reports.
© 2024 PatSnap. All rights reserved.Legal|Privacy policy|Modern Slavery Act Transparency Statement|Sitemap|About US| Contact US: help@patsnap.com