Method for preparing graphene oxide grafted with thermotropic liquid crystal compound with end group containing epoxy group
A liquid crystal compound, thermotropic technology, applied in the field of material chemistry, can solve the problems of difficult mass production and application, complex operation process and high cost, and achieve the effects of improved mechanical and thermal properties, simple process and low pollution.
- Summary
- Abstract
- Description
- Claims
- Application Information
AI Technical Summary
Problems solved by technology
Method used
Examples
Embodiment 1
[0020] (1) Weigh 2 grams of terephthaloyl chloride and 1.5 grams of p-hydroxybenzoic acid into 15 milliliters of N,N-dimethylformamide (DMF) solvent, add 0.05 g of pyridine as a catalyst dropwise, and place under magnetic stirring React at 80°C for 6 hours; add 8 ml of thionyl chloride (SOCl 2 ) to continue the reaction for 12 hours; add 3 grams of diethylene glycol to continue the reaction for 6 hours; add 2.5 grams of glycidyl alcohol, drop 0.2g butyltin dilaurate as a catalyst, and continue the reaction for 6 hours. After the reaction, Precipitate the product with a large amount of water, filter it under reduced pressure, wash the product three times with absolute ethanol, and dry it to obtain a milky white thermotropic liquid crystal compound containing epoxy groups at the end.
[0021] (2) Mix 0.1 g of graphite oxide and 50 ml of N,N-dimethylformamide (DMF), and disperse in an ultrasonic environment for 60 minutes to form a uniformly dispersed graphene oxide mixed solutio...
Embodiment 2
[0026] (1) Weigh 2 grams of terephthaloyl chloride and 3 grams of p-hydroxybenzoic acid and add them to 15 ml of N,N-dimethylformamide (DMF) solvent, add 0.1 g of pyridine as a catalyst dropwise, and place under magnetic stirring React at 80°C for 6 hours; add 10 ml of thionyl chloride (SOCl 2 ) to continue the reaction for 24 hours; add 4 grams of diethylene glycol and continue the reaction for 6 hours; then add 3.5 grams of glycidyl alcohol, add dropwise 0.3 g of butyltin dilaurate as a catalyst, and continue the reaction for 6 hours. After the reaction, Precipitate the product with a large amount of water, filter it under reduced pressure, wash the product three times with absolute ethanol, and dry it to obtain a milky white thermotropic liquid crystal compound containing epoxy groups at the end.
[0027] (2) Mix 0.1 g of graphite oxide and 50 ml of N,N-dimethylformamide (DMF) and disperse in an ultrasonic environment for 90 minutes to form a uniformly dispersed graphene ox...
Embodiment 3
[0032](1) Weigh 4 grams of terephthaloyl chloride and 1.5 grams of p-hydroxybenzoic acid into 15 milliliters of N,N-dimethylformamide (DMF) solvent, add 0.1 g of pyridine as a catalyst dropwise, and place under magnetic stirring React at 80°C for 6 hours; add 8 ml of thionyl chloride (SOCl 2 ) to continue the reaction for 24 hours; add 3 grams of diethylene glycol to continue the reaction for 6 hours; add 2.5 grams of glycidyl alcohol, drop 0.5g butyltin dilaurate as a catalyst, and continue the reaction for 6 hours. After the reaction, Precipitate the product with a large amount of water, filter it under reduced pressure, wash the product three times with absolute ethanol, and dry it to obtain a milky white thermotropic liquid crystal compound containing epoxy groups at the end.
[0033] (2) Mix 0.1 g of graphite oxide and 50 ml of N,N-dimethylformamide (DMF) and disperse in an ultrasonic environment for 120 minutes to form a uniformly dispersed graphene oxide mixed solution....
PUM
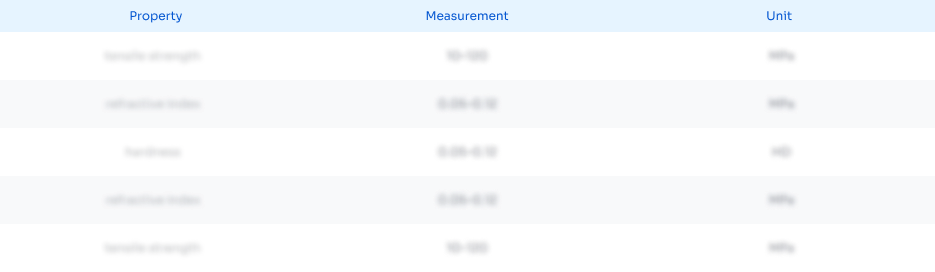
Abstract
Description
Claims
Application Information

- R&D
- Intellectual Property
- Life Sciences
- Materials
- Tech Scout
- Unparalleled Data Quality
- Higher Quality Content
- 60% Fewer Hallucinations
Browse by: Latest US Patents, China's latest patents, Technical Efficacy Thesaurus, Application Domain, Technology Topic, Popular Technical Reports.
© 2025 PatSnap. All rights reserved.Legal|Privacy policy|Modern Slavery Act Transparency Statement|Sitemap|About US| Contact US: help@patsnap.com