Method for rising superheated steam temperature of concurrent boiler during pipe blowing
A technology of superheated steam and once-through boiler, which is applied in the direction of steam superheating, steam generation, lighting and heating equipment, etc., to save blowing time, save fuel, and save costs
- Summary
- Abstract
- Description
- Claims
- Application Information
AI Technical Summary
Problems solved by technology
Method used
Image
Examples
Embodiment
[0017] Embodiment: the connection structure of each device of this system is as follows figure 1 As shown, the main devices of the system are water wall 1, water storage tank discharge valve 2, superheater 3, superheater trap 4, steam turbine 5, blowpipe control valve 6, reheater 7, and the connected pipes and valves.
[0018] When the system connection is normal, during the gap between the two blowpipes, use the method of water-cooled wall exchange or superheater exhaust to control the pressure increase speed of the steam-water system to ensure that the heating surface of the superheater has enough heating time to improve The temperature of the superheated steam meets the requirement that there is a higher temperature of the superheated steam when blowing the pipe.
[0019] The operation method is to use one or both of method a or method b:
[0020] The method a is to replace the high-temperature water with low-temperature water to reduce steam discharge and control the pres...
PUM
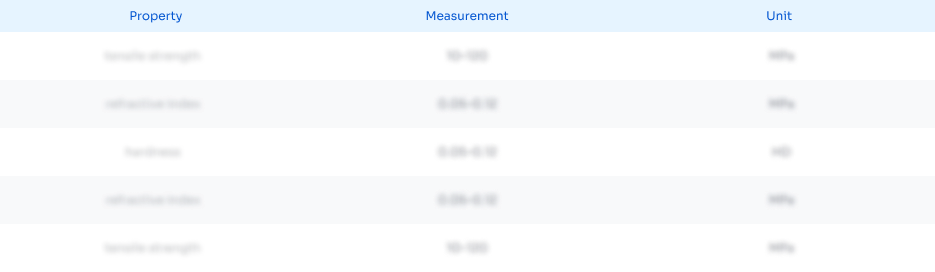
Abstract
Description
Claims
Application Information

- R&D Engineer
- R&D Manager
- IP Professional
- Industry Leading Data Capabilities
- Powerful AI technology
- Patent DNA Extraction
Browse by: Latest US Patents, China's latest patents, Technical Efficacy Thesaurus, Application Domain, Technology Topic, Popular Technical Reports.
© 2024 PatSnap. All rights reserved.Legal|Privacy policy|Modern Slavery Act Transparency Statement|Sitemap|About US| Contact US: help@patsnap.com