Method for dissolving Bayer process red mud
A Bayer method red mud and solution technology, applied in chemical instruments and methods, sludge treatment, water/sludge/sewage treatment, etc., can solve the problems of low comprehensive utilization rate and high cost of valuable components, and achieve total value High, improve environmental protection standards, reduce the effect of CO2 gas
- Summary
- Abstract
- Description
- Claims
- Application Information
AI Technical Summary
Problems solved by technology
Method used
Image
Examples
Embodiment 1
[0031] Mix red mud and slaked lime at a mass ratio of 1:0.3, then stir at 120°C for calcification transformation and dealkalization reaction for 1.5 hours. After the reaction, the alkali content in red mud is reduced to below 2%, and then the main components after clean water and calcification transformation are The red mud of hydrated garnet is mixed in a closed container according to the liquid-solid ratio of 3:1, and the partial pressure is 1.6MPa, and the volume concentration is 100% CO at 120°C. 2 The gas reacted for 10 minutes, and the calcified red mud was converted into carbonized slag whose main components were aluminum hydroxide, calcium carbonate and calcium silicate after carbonization transformation.
[0032]Use a NaOH solution with a concentration of 30g / L to extract the aluminum hydroxide in the carbonized slag under the conditions of a dissolution temperature of 100°C and a liquid-solid ratio of (10:1) mL / g, and obtain a new structure of red mud by alkali dissol...
Embodiment 2
[0034] Mix red mud and slaked lime at a mass ratio of 1:0.9, then stir at 140°C for calcification and dealkalization reaction for 1.0h. After the reaction, the alkali content in red mud is reduced to less than 1%, and then the main components after clean water and calcification transformation are The red mud of hydrated garnet is mixed in a closed container according to the liquid-solid ratio of 15:1, and the partial pressure is 1.2MPa, and the volume concentration is 10% CO at 120°C. 2 The gas reacts for 30 minutes, and the calcified red mud is converted into carbonized slag whose main components are aluminum hydroxide, calcium carbonate and calcium silicate after carbonization transformation.
[0035] Use the NaOH solution with a concentration of 100g / L to extract the aluminum hydroxide in the carbonized slag under the conditions of a dissolution temperature of 60°C and a liquid-solid ratio of (15:1) mL / g, and obtain a new structure of red mud by alkali dissolution The main ...
Embodiment 3
[0037] Mix the red mud and slaked lime at a mass ratio of 1:0.6, and then stir the calcification transformation dealkalization reaction at 120°C for 8 hours. After the reaction, the alkali content in the red mud is reduced to below 2%, and then the Na 2 Sodium aluminate solution with an O mass content of 10g / L and red mud whose main component is hydrated garnet after calcification transformation are mixed in a closed container at a liquid-solid ratio of 10:1, and the partial pressure is introduced at 80°C. 0.6MPa, the volume concentration is 50% CO 2 The gas reacted for 60 minutes, and the calcified red mud was converted into carbonized slag whose main components were aluminum hydroxide, calcium carbonate and calcium silicate after carbonization transformation.
[0038] Use a solution with a NaOH concentration of 30g / L to extract the aluminum hydroxide in the carbonized slag under the conditions of a dissolution temperature of 100°C and a liquid-solid ratio of (15:1) mL / g, and...
PUM
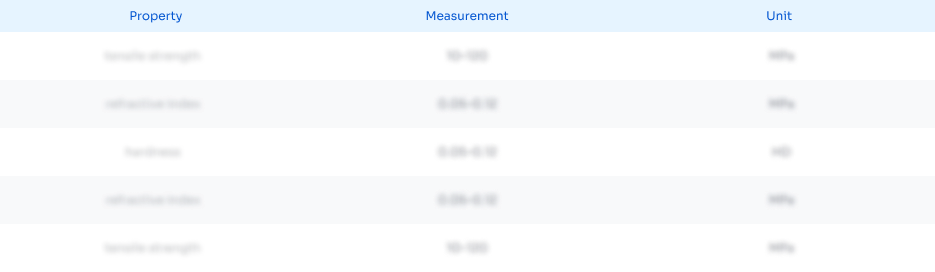
Abstract
Description
Claims
Application Information

- R&D
- Intellectual Property
- Life Sciences
- Materials
- Tech Scout
- Unparalleled Data Quality
- Higher Quality Content
- 60% Fewer Hallucinations
Browse by: Latest US Patents, China's latest patents, Technical Efficacy Thesaurus, Application Domain, Technology Topic, Popular Technical Reports.
© 2025 PatSnap. All rights reserved.Legal|Privacy policy|Modern Slavery Act Transparency Statement|Sitemap|About US| Contact US: help@patsnap.com