Space decoupling three-dimensional motion parallel micro-motion mechanism
A three-dimensional moving and moving mechanism technology, applied in manipulators, program-controlled manipulators, manufacturing tools, etc., can solve the problems of small operation space and poor motion decoupling, so as to expand the working space, overcome the problem of motion coupling, and solve the problem of working space. The effect of restriction
- Summary
- Abstract
- Description
- Claims
- Application Information
AI Technical Summary
Problems solved by technology
Method used
Image
Examples
Embodiment Construction
[0017] The specific implementation manners of the present invention will be further described in detail below in conjunction with the accompanying drawings and embodiments. The following examples are used to illustrate the present invention, but are not intended to limit the scope of the present invention.
[0018] The structure of a space-decoupled three-dimensional mobile parallel micro-motion mechanism in an embodiment of the present invention is as follows: figure 1 As shown, it includes a base platform 1, a moving platform 2, three branches 3 and three piezoelectric ceramic drivers 4 respectively installed on the three branches 3; the three branches 3 are mutually orthogonal and installed on the On the base platform 1 and connected with the moving platform 2. The branch structure of the embodiment of the present invention is as follows figure 2 As shown, it includes a flexible rotating pair 5, a flexible moving pair 7 and a flexible cylindrical pair 9, and the flexible...
PUM
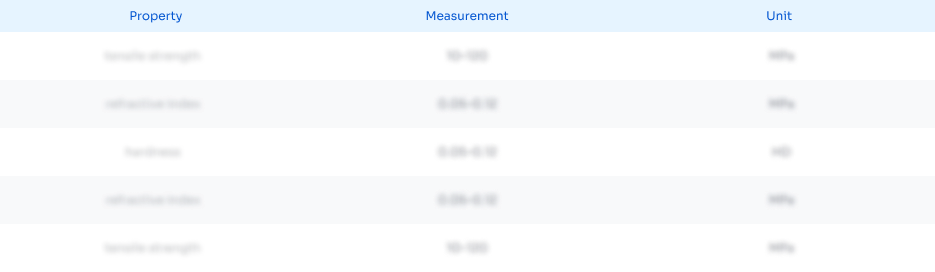
Abstract
Description
Claims
Application Information

- Generate Ideas
- Intellectual Property
- Life Sciences
- Materials
- Tech Scout
- Unparalleled Data Quality
- Higher Quality Content
- 60% Fewer Hallucinations
Browse by: Latest US Patents, China's latest patents, Technical Efficacy Thesaurus, Application Domain, Technology Topic, Popular Technical Reports.
© 2025 PatSnap. All rights reserved.Legal|Privacy policy|Modern Slavery Act Transparency Statement|Sitemap|About US| Contact US: help@patsnap.com