Light foot lead welding machine of bulb in bulb
A technology of lamp pin lead wire and bubble in bubble, which is applied in the field of lamp pin lead wire welding machine, which can solve the problems of manual work, unstable welding quality, and prone to industrial accidents, etc., and achieve the effect of improving stability
- Summary
- Abstract
- Description
- Claims
- Application Information
AI Technical Summary
Problems solved by technology
Method used
Image
Examples
Embodiment 1
[0086] Such as Figure 4 and Figure 5 As shown, a welding machine for lamp pin leads of a bulb in a bulb includes a base frame 1, a driving power device arranged on the base frame 1, a tray 11 driven forward by the driving power device, The central controller 121 arranged on the chassis 1 and the clamping device 2 arranged on the tray 11 .
[0087] The driving power device includes a cam splitter 12 and a motor and reduction gear box assembly 123 for driving the cam splitter 12 .
[0088] A separate synchronous output shaft 122 is also arranged on the cam divider 12 of the driving power unit, an angle encoder 124 is connected with the output shaft 122, and the angle encoder 124 is connected with the central controller 121 connect. In this way, the angular displacement of the output shaft 122 and the angular displacement of the pallet 11 have a fixed proportional relationship, and the angle encoder 124 can indirectly sample the angular displacement of the pallet 11, so that...
Embodiment 2
[0137] The difference from Example 1 is:
[0138] 1. The tray 11 is provided with 8 first chucks 21 that can only hold the lamp cap a, while the stem b is transported by the stem manipulator 32 of the stem feeding station 3 but not clamped in the The structure of the first clip 21 on the tray 11 can adopt the structure disclosed in Embodiment 1, or other structures, as long as it can hold the lamp cap a.
[0139] 2. The stem feeding station 3 is set as the lower station of the lamp cap feeding station 4;
[0140] 3. The stem manipulator 32 of the stem feeding station 3 grabs the stem b from the stem automatic feeder 31 and then sends the stem b to the vicinity of the position of the corresponding first chuck 21 and makes it The lamp pin leads (b1, b2) of the stem b correspond to and partially overlap with the lamp pin leads (a1, a2) of the lamp cap a clamped in the first chuck 21, but the stem manipulator 32 The pin lead does not release the stem b until a solder joint is...
Embodiment 3
[0146] The difference from Example 1 is:
[0147] 1. Eight second grippers 22 that can only clamp the stem b are arranged on the tray 11; while the lamp cap a is transported by the stem manipulator 42 of the lamp cap feeding station 4 but is not clamped in the on the tray 11; the structure of the second chuck 22 can adopt the structure disclosed in the first embodiment, or other structures, as long as it can clamp the stem b.
[0148] 2. The lamp cap manipulator 42 of the lamp cap feeding station 4 grabs the lamp cap a from the lamp cap automatic feeder 41 and sends the lamp cap a to the vicinity of the corresponding position of the second chuck 22 and makes the lamp pin of the lamp cap a The lead wires (a1, a2) correspond to and partially coincide with the lamp pin leads (b1, b2) of the stem b clamped in the second clamp 22, but the lamp cap manipulator 42 completes a welding spot on the lamp pin lead Previously, lamp head a was not released.
[0149] 3. A welding statio...
PUM
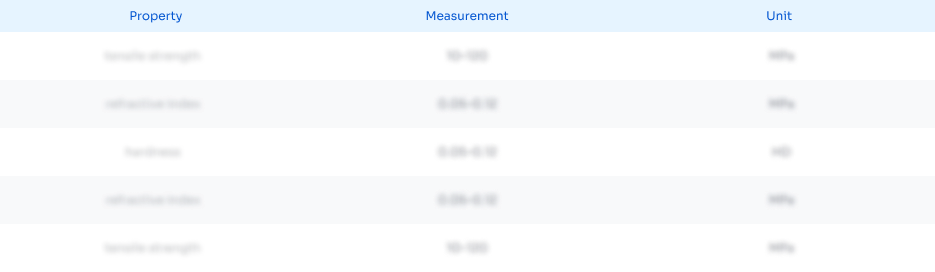
Abstract
Description
Claims
Application Information

- Generate Ideas
- Intellectual Property
- Life Sciences
- Materials
- Tech Scout
- Unparalleled Data Quality
- Higher Quality Content
- 60% Fewer Hallucinations
Browse by: Latest US Patents, China's latest patents, Technical Efficacy Thesaurus, Application Domain, Technology Topic, Popular Technical Reports.
© 2025 PatSnap. All rights reserved.Legal|Privacy policy|Modern Slavery Act Transparency Statement|Sitemap|About US| Contact US: help@patsnap.com