Optimized design method for determining geometric parameters of intermediate construction for forming panel veneer in multiple steps
A technology of geometric parameters and optimal design, applied in the fields of calculation, electrical digital data processing, special data processing applications, etc., can solve the problems of poor accuracy and difficulty in obtaining the optimal values of geometric parameters of intermediate configurations.
- Summary
- Abstract
- Description
- Claims
- Application Information
AI Technical Summary
Problems solved by technology
Method used
Image
Examples
Embodiment 1
[0034] Example 1: figure 1 It is a CAD model of a rectangular local feature part, and the specific outline dimensions are: length 200mm, width 200mm, thickness 0.8mm. The material is SECCN5, the elastic modulus is 210Mpa, the Poisson's ratio is 0.28, the hardening index n=0.1825, and the thickness anisotropy coefficient r=1.662. Since the part is extracted from a back plate part, the blank-holding force of the back plate part cannot be adjusted during the forming process, so the blank-holding force of the rectangular local feature part cannot be adjusted during the forming process. Cracking occurs, and multi-step forming is required to solve the cracking problem.
[0035] figure 2 A flow chart of an optimal design method for determining the geometric parameters of the intermediate configuration of the multi-step forming of the sheet metal is shown in the present invention. The optimal design method of the geometric parameters of the intermediate configuration for determini...
PUM
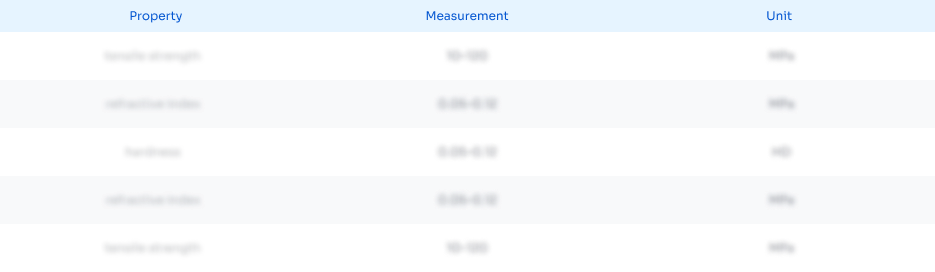
Abstract
Description
Claims
Application Information

- Generate Ideas
- Intellectual Property
- Life Sciences
- Materials
- Tech Scout
- Unparalleled Data Quality
- Higher Quality Content
- 60% Fewer Hallucinations
Browse by: Latest US Patents, China's latest patents, Technical Efficacy Thesaurus, Application Domain, Technology Topic, Popular Technical Reports.
© 2025 PatSnap. All rights reserved.Legal|Privacy policy|Modern Slavery Act Transparency Statement|Sitemap|About US| Contact US: help@patsnap.com