Anhydrous phosphoric acid/phosphate solvent and application thereof in dissolving cellulose
A technology for dissolving cellulose and anhydrous phosphoric acid, which is applied in the preparation of artificial filaments and spinning solutions in cellulose solutions, can solve the problems of expensive solvents, environmental pollution, flammable and explosive, etc., and achieve solvent recovery. Simple, solve the problem of environmental pollution, the effect of low price
- Summary
- Abstract
- Description
- Claims
- Application Information
AI Technical Summary
Problems solved by technology
Method used
Examples
Embodiment 1
[0027] Weigh 9.8 grams of anhydrous phosphoric acid and 0.47-2.82 grams of trimethyl phosphate. Add trimethyl phosphate dropwise to anhydrous phosphoric acid. After the dropwise addition, stir slowly until the anhydrous phosphoric acid is completely dissolved. Weigh 8 grams of the above-prepared solvent, place it in a heating mantle and raise the temperature to 30° C. to keep it warm. Weigh 1 gram of cotton fiber, add the cotton fiber to the solvent little by little, and then stir until the cellulose is completely dissolved. The cellulose solution is placed in a high-speed centrifuge to remove the air, and the obtained solution is spun through a spinning machine using wet spinning technology. After being solidified by the solidifying liquid, it is washed several times to obtain regenerated cellulose.
Embodiment 2
[0029] Weigh 9.8 grams of anhydrous phosphoric acid and 0.42 to 2.52 grams of dimethyl phosphate. Dimethyl phosphate was added dropwise to anhydrous phosphoric acid. After the dropwise addition, stir slowly until the anhydrous phosphoric acid is completely dissolved. Weigh 8 grams of the above-prepared solvent, place it in a heating mantle and raise the temperature to 30° C. to keep it warm. Weigh 1 gram of cotton fiber, add the cotton fiber to the solvent little by little, and then stir until the cellulose is completely dissolved. The cellulose solution is placed in a high-speed centrifuge to remove the air, and the obtained solution is spun through a spinning machine using wet spinning technology. After being solidified by the solidifying liquid, it is washed several times to obtain regenerated cellulose.
Embodiment 3
[0031] Weigh 9.8 grams of anhydrous phosphoric acid and 0.61 to 3.63 grams of monomethyl phosphate. Add triethyl phosphate dropwise to anhydrous phosphoric acid. After the dropwise addition, stir slowly until the anhydrous phosphoric acid is completely dissolved. Weigh 5 grams of the prepared solvent, place it in a heating mantle and raise the temperature to 40° C. to keep it warm. Weigh 1 gram of cotton fiber, add the cotton fiber to the solvent little by little, and then stir until the cellulose is completely dissolved. The cellulose solution is placed in a high-speed centrifuge to remove the air, and the obtained solution is spun through a spinning machine using wet spinning technology. After being solidified by the solidifying liquid, it is washed several times to obtain regenerated cellulose.
PUM
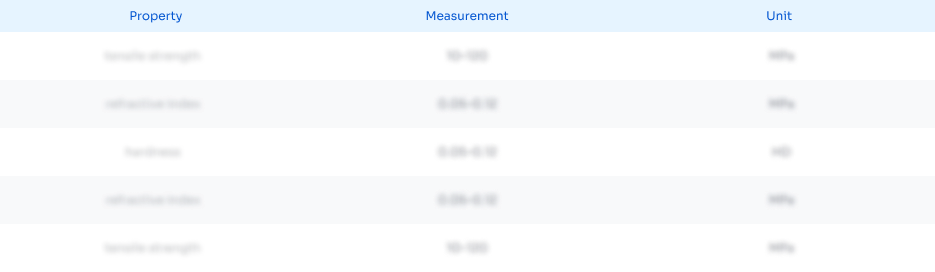
Abstract
Description
Claims
Application Information

- Generate Ideas
- Intellectual Property
- Life Sciences
- Materials
- Tech Scout
- Unparalleled Data Quality
- Higher Quality Content
- 60% Fewer Hallucinations
Browse by: Latest US Patents, China's latest patents, Technical Efficacy Thesaurus, Application Domain, Technology Topic, Popular Technical Reports.
© 2025 PatSnap. All rights reserved.Legal|Privacy policy|Modern Slavery Act Transparency Statement|Sitemap|About US| Contact US: help@patsnap.com