Hammer forging device for forming complicated long-axis forgings applied to radial forging machine
A radial forging, long-axis technology, used in forging/pressing/hammer devices, engine components, forging/pressing/hammering machinery, etc., can solve problems beyond the capabilities of existing equipment, inability to form local features, difficult to carry out, etc. question
- Summary
- Abstract
- Description
- Claims
- Application Information
AI Technical Summary
Problems solved by technology
Method used
Image
Examples
Embodiment
[0032] A hammer forging device used for forming complex long-shaft forgings on a radial forging machine, its structure is as follows figure 1 As shown, it is mainly composed of the following components: a forging unit installed on the hammer head of each radial forging machine. The other parts of each forging unit are the same except for the forming module. Its structure includes: forming module 1, dynamic Mold base 2, fixed mold base 3, template 14, compression block control assembly 4, compression block 5, compression block control assembly fixing plate 6, gear mounting seat 9, etc. Radial forging machines generally use 4 hammerheads, and this example also uses 4 hammerheads, which are respectively installed in the forming modules 1 of the 4 forging units to form plastic deformation zones.
[0033] The structures of several main components of the present invention are described in detail below.
[0034] The fixed die base 3 includes the following structure: there are 4 moun...
PUM
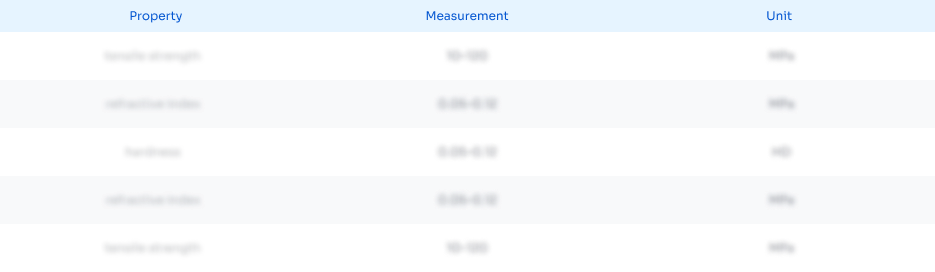
Abstract
Description
Claims
Application Information

- R&D
- Intellectual Property
- Life Sciences
- Materials
- Tech Scout
- Unparalleled Data Quality
- Higher Quality Content
- 60% Fewer Hallucinations
Browse by: Latest US Patents, China's latest patents, Technical Efficacy Thesaurus, Application Domain, Technology Topic, Popular Technical Reports.
© 2025 PatSnap. All rights reserved.Legal|Privacy policy|Modern Slavery Act Transparency Statement|Sitemap|About US| Contact US: help@patsnap.com