Method for preparing nitro orotic acid
A technology of nitroorotic acid and nitro, which is applied in the field of preparation of nitroorotic acid and compounds, can solve problems such as reaction system explosion, and achieve the effect of reducing risk and safety advantages
- Summary
- Abstract
- Description
- Claims
- Application Information
AI Technical Summary
Problems solved by technology
Method used
Image
Examples
Embodiment 1
[0029] The preparation of embodiment 1 nitroorotic acid
[0030] Mix and stir 1.8kg (18.18mol) of concentrated sulfuric acid (98%) and 17kg (142.9mol) of chloroform, then add 1.5kg (11.6mol) of 6-methyluracil at one time and heat up to 50°C. Control the temperature at 50-55°C, add 9 kg (140 mol) of concentrated nitric acid (98%) dropwise to the mixture, and after the dropwise addition, reflux and stir at this temperature for 30 hours (the reaction is complete as detected by HPLC).
[0031] Stop heating after the reaction is complete, add 3kg of water into the system, keep the system temperature not exceeding 35°C, separate layers, and the chloroform layer can be directly recycled and reused.
[0032] The water layer was cooled to 1-5°C, kept at this temperature for 3 hours, then suction filtered and dried to obtain the product.
[0033] Yield: 1.96kg (84.1%);
[0034] Purity: 97.6% (HPLC).
Embodiment 2
[0035] The preparation of embodiment 2 nitroorotic acid
[0036] Mix and stir 1.8kg (18.18mol) of concentrated sulfuric acid (98%) and 17kg (142.9mol) of chloroform, then add 1.5kg (11.6mol) of 6-methyluracil at one time and heat up to 50°C. Control the temperature at 50-55°C, add 4.5kg (70mol) of concentrated nitric acid (98%) dropwise to the mixture, and after the dropwise addition, reflux and stir at this temperature for 30 hours (the reaction is complete as detected by HPLC).
[0037] Stop heating after the reaction is complete, add 3kg of water into the system, keep the system temperature not exceeding 35°C, separate layers, and the chloroform layer can be directly recycled and reused.
[0038] The water layer was cooled to 1-5°C, kept at this temperature for 3 hours, then suction filtered and dried to obtain the product.
[0039] Yield: 1.31kg (56%);
[0040] Purity: 97.0% (HPLC).
Embodiment 3
[0041] The preparation of embodiment 3 nitroorotic acid
[0042] Mix and stir 1.8kg (18.18mol) of concentrated sulfuric acid (98%) and 17kg (142.9mol) of chloroform, then add 1.5kg (11.6mol) of 6-methyluracil at one time and heat up to 50°C. Control the temperature at 50-55°C, add 10.5kg (163mol) of concentrated nitric acid (98%) dropwise to the mixture, and after the dropwise addition, reflux and stir at this temperature for 30 hours (HPLC detects that the reaction is complete).
[0043] Stop heating after the reaction is complete, add 3kg of water into the system, keep the system temperature not exceeding 35°C, separate layers, and the chloroform layer can be directly recycled and reused.
[0044] The water layer was cooled to 1-5°C, kept at this temperature for 3 hours, then suction filtered and dried to obtain the product.
[0045] Yield: 1.86kg (80.1%);
[0046] Purity: 97.7% (HPLC).
PUM
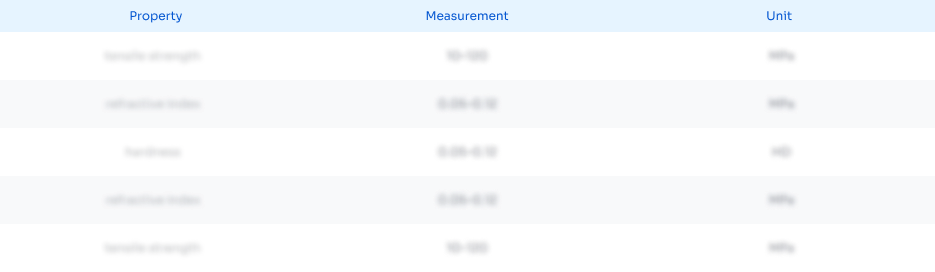
Abstract
Description
Claims
Application Information

- R&D
- Intellectual Property
- Life Sciences
- Materials
- Tech Scout
- Unparalleled Data Quality
- Higher Quality Content
- 60% Fewer Hallucinations
Browse by: Latest US Patents, China's latest patents, Technical Efficacy Thesaurus, Application Domain, Technology Topic, Popular Technical Reports.
© 2025 PatSnap. All rights reserved.Legal|Privacy policy|Modern Slavery Act Transparency Statement|Sitemap|About US| Contact US: help@patsnap.com