Method for calibrating strain parameters of optical fiber sensor and optical fiber grating
A fiber optic sensor and fiber grating technology, which is applied to instruments, optical devices, measuring devices, etc., can solve the problems of narrow measurement range, low measurement accuracy, and difficulty in meeting measurement requirements.
- Summary
- Abstract
- Description
- Claims
- Application Information
AI Technical Summary
Problems solved by technology
Method used
Image
Examples
Embodiment Construction
[0019] The preferred embodiments of the present invention will be described in detail below in conjunction with the accompanying drawings; it should be understood that the preferred embodiments are only for illustrating the present invention, rather than limiting the protection scope of the present invention.
[0020] The method adopts a displacement measurement method, and combines a precision displacement sensor and an optical fiber sensor to produce a standard transmission part to generate a standard strain value, thereby indirectly achieving the calibration of the optical fiber sensor and the optical fiber grating strain parameters. Optical fiber strain transmission parts mainly include "concave" optical bracket 2, standard optical fiber sensor 3, precision displacement sensor 5, displacement sensor controller, etc. The "concave" shaped optical bracket 2 is composed of an optical slide rail guide groove, a fixed end 1 and a free end 4. There are "V" grooves engraved on the...
PUM
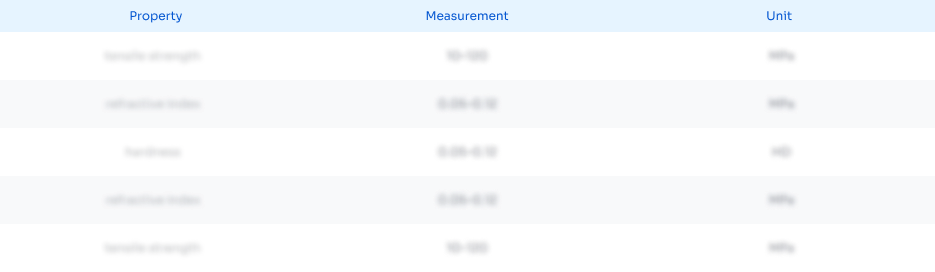
Abstract
Description
Claims
Application Information

- R&D
- Intellectual Property
- Life Sciences
- Materials
- Tech Scout
- Unparalleled Data Quality
- Higher Quality Content
- 60% Fewer Hallucinations
Browse by: Latest US Patents, China's latest patents, Technical Efficacy Thesaurus, Application Domain, Technology Topic, Popular Technical Reports.
© 2025 PatSnap. All rights reserved.Legal|Privacy policy|Modern Slavery Act Transparency Statement|Sitemap|About US| Contact US: help@patsnap.com