Method for coloring surface of ceramic body and ceramic colorant
A technology for ceramic body and surface coloring, applied in the field of ceramic materials, can solve the problems of unclear concave and convex contours of the die surface, poor imitation stone effect, color limitation of glaze, etc., and achieve a realistic imitation stone effect, low cost and delicate texture. Effect
- Summary
- Abstract
- Description
- Claims
- Application Information
AI Technical Summary
Problems solved by technology
Method used
Image
Examples
Embodiment 1
[0043] Such as figure 1 Shown, the invention provides a kind of method for coloring the surface of ceramic body, the method comprises the steps:
[0044] 1. Preparation of ceramic body
[0045] Configure the green body raw materials, where K 2 O and Na 2 The content of O is controlled at 4.0% to 6.0% of the weight percentage of the total ceramic body raw material; K 2 O: Na 2 O=1:0.8~1:2; the CaO content is controlled below 1.5% by weight of the total ceramic body raw materials; the MgO content is controlled below 1.5% by weight of the total ceramic body raw materials.
[0046] Perform ball milling and pulping on the configured green body raw materials;
[0047] To test the mud;
[0048] Spray and granulate the slurry;
[0049] Detect the powder formed after granulation;
[0050] The qualified powder is pressed into a ceramic green body.
[0051] 2. Atomize and spray the coloring agent on the surface of the ceramic body. The raw materials of the coloring agent are tap...
Embodiment 2
[0067] 1. Preparation of ceramic body
[0068] Configure the green body raw materials, where K 2 O and Na 2 The content of O is controlled at 4.0% to 6.0% of the weight percentage of the total ceramic body raw material; K 2 O: Na 2 O=1:0.8~1:2; the CaO content is controlled below 1.2% by weight of the total ceramic body raw materials; the MgO content is controlled below 1.2% by weight of the total ceramic body raw materials.
[0069] Perform ball milling and pulping on the configured green body raw materials;
[0070] To test the mud;
[0071] Spray and granulate the slurry;
[0072] Detect the powder formed after granulation;
[0073] The qualified powder is pressed into a ceramic green body.
[0074] 2. Atomize and spray the colorant on the surface of the ceramic body. The raw materials of the colorant are factory circulating water, chemical materials, ceramic colorants and suspension stabilizers. The chemical materials are quartz and zirconium silicate, and the ceram...
Embodiment 3
[0086] 1. Preparation of ceramic body
[0087] Configure the green body raw materials, where K 2 O and Na 2 The content of O is controlled at 4.0% to 6.0% of the weight percentage of the total ceramic body raw material; K 2 O: Na 2 O=1:0.8~1:2; the CaO content is controlled below 1.0% by weight of the total ceramic body raw materials; the MgO content is controlled below 1.0% by weight of the total ceramic body raw materials.
[0088] Perform ball milling and pulping on the configured green body raw materials;
[0089] To test the mud;
[0090] Spray and granulate the slurry;
[0091] Detect the powder formed after granulation;
[0092] The qualified powder is pressed into a ceramic green body.
[0093] 2. Atomize and spray the colorant on the surface of the ceramic body. The raw materials of the colorant are river water, chemical materials, ceramic colorants and suspension stabilizers. The chemical materials are frits, and the ceramic colorants are water-insoluble color...
PUM
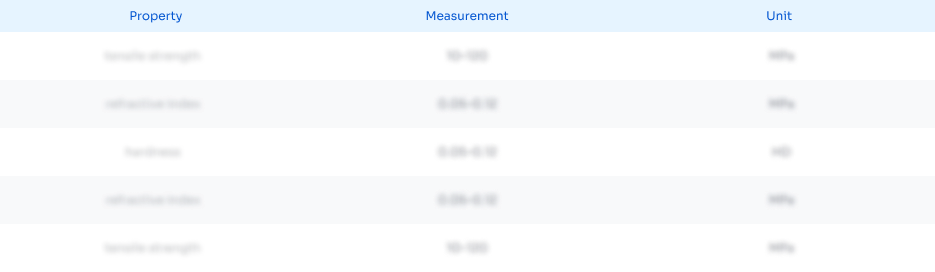
Abstract
Description
Claims
Application Information

- R&D
- Intellectual Property
- Life Sciences
- Materials
- Tech Scout
- Unparalleled Data Quality
- Higher Quality Content
- 60% Fewer Hallucinations
Browse by: Latest US Patents, China's latest patents, Technical Efficacy Thesaurus, Application Domain, Technology Topic, Popular Technical Reports.
© 2025 PatSnap. All rights reserved.Legal|Privacy policy|Modern Slavery Act Transparency Statement|Sitemap|About US| Contact US: help@patsnap.com