Building ecological heat-insulation mortar and preparation method thereof
A thermal insulation mortar and building technology, applied in the field of ecological thermal insulation mortar, can solve the problems of packaging, storage and transportation, and the inconvenience of the construction process, and achieve the effects of reduced maintenance burden, simple production process, light weight and high strength specific surface area
- Summary
- Abstract
- Description
- Claims
- Application Information
AI Technical Summary
Problems solved by technology
Method used
Examples
preparation example Construction
[0017] The preparation method of building ecological thermal insulation mortar of the present invention is carried out according to the following steps:
[0018] (1) Making phase change materials: Mix solid paraffin, white oil and vaseline at 1:1:0.5, heat and stir for 30 minutes, and then make a round solid with a softening point of 18-26°C and a diameter of 1-4mm. Coated for later use.
[0019] (2) Making foaming agent: Mix ammonium bicarbonate and sodium bicarbonate at a ratio of 1:1 for later use.
[0020] (3) 1-40 parts of the phase change material obtained in (1) and 1-10 parts of the foaming agent obtained in (2) are mixed with 40-90 parts of sulphoaluminate cement, fly ash or ground water-quenched slag 1 -40, 1-30 parts of activated carbon or bamboo charcoal, 1-30 parts of high-strength gypsum or building gypsum, 1-40 parts of closed-cell perlite, 0.1-1.5 parts of methyl cellulose, 0.1-2 parts of waterproofing agent, mix and pack evenly finished product. When in use...
Embodiment 1
[0022] In the building ecological thermal insulation mortar of the present invention, the raw material ratio of the inner wall thermal insulation mortar is: 15 parts of phase change material, 40 parts of sulfoaluminate cement, 5 parts of foaming agent, 5 parts of fly ash, 15 parts of activated carbon or bamboo charcoal 15 parts of construction gypsum, 4 parts of closed-cell perlite, 0.8 parts of methyl cellulose, and 0.2 parts of waterproofing agent.
[0023] The preparation steps of interior wall insulation mortar are:
[0024] (1) Making phase change materials: Mix solid paraffin, white oil and vaseline at 1:1:0.5, heat and stir for 30 minutes, and then make a round solid with a softening point of 18-26°C and a diameter of 1-4mm. Coated for later use.
[0025] (2) Making foaming agent: Mix ammonium bicarbonate and sodium bicarbonate at a ratio of 1:1 for later use.
[0026] (3) Combine 15 parts of the phase change material obtained in (1) and 5 parts of the foaming agent o...
Embodiment 2
[0028] In the building ecological thermal insulation mortar of the present invention, the raw material ratio of the external wall thermal insulation mortar is: 12.5 parts of phase change material, 50 parts of sulfoaluminate cement, 4 parts of foaming agent, 10 parts of ground water-quenched slag, 5 parts of bamboo charcoal 10 parts of high-strength gypsum, 5 parts of closed-cell perlite, 1.5 parts of methyl cellulose, and 2 parts of waterproofing agent.
[0029] The preparation steps of the external wall insulation mortar are:
[0030] (1) Making phase change materials: Mix solid paraffin, white oil and vaseline at 1:1:0.5, heat and stir for 30 minutes, and then make a round solid with a softening point of 18-26°C and a diameter of 1-4mm. Coated for later use.
[0031] (2) Making foaming agent: Mix ammonium bicarbonate and sodium bicarbonate at a ratio of 1:1 for later use.
[0032] (3) Combine 12.5 parts of the phase change material obtained in (1) and 4 parts of the foamin...
PUM
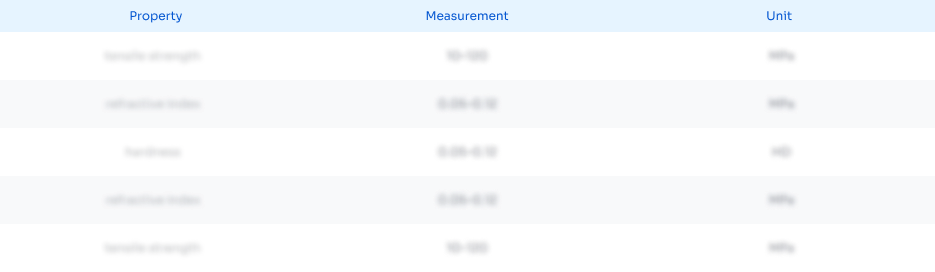
Abstract
Description
Claims
Application Information

- R&D
- Intellectual Property
- Life Sciences
- Materials
- Tech Scout
- Unparalleled Data Quality
- Higher Quality Content
- 60% Fewer Hallucinations
Browse by: Latest US Patents, China's latest patents, Technical Efficacy Thesaurus, Application Domain, Technology Topic, Popular Technical Reports.
© 2025 PatSnap. All rights reserved.Legal|Privacy policy|Modern Slavery Act Transparency Statement|Sitemap|About US| Contact US: help@patsnap.com