Three-axis linkage contour error compensation control method for cylinder cam machining
A contour error, cylindrical cam technology, applied in the direction of program control, computer control, general control system, etc., can solve the distance contour error of tangent line, the difficulty of description and calculation and compensation, the calculation method of contour error, the lack of research on compensation method and other problems , to achieve the effect of high calculation accuracy and simple calculation method
- Summary
- Abstract
- Description
- Claims
- Application Information
AI Technical Summary
Problems solved by technology
Method used
Image
Examples
Embodiment Construction
[0020] For the simultaneous machining of cylindrical cams with A-axis, X-axis, and Y-axis, the following combination Figure 1~4 The present invention is described in further detail:
[0021] 1) if figure 2 As shown, when using the A-axis, X-axis, and Y-axis to process the cylindrical cam, the X linear axis is perpendicular to the Y linear axis, and the A axis is the rotation axis around the X axis, so as to establish the machine tool coordinate system; the established space Cartesian coordinates In the Oxyz system, in addition to the X linear axis and Y linear axis of simultaneous machining, the Z linear axis is also virtualized, and the X axis, Y axis, and Z axis conform to the right-handed Cartesian coordinate system.
[0022] In each sampling period of the interpolation processing of the tool track of the cylindrical cam contour line, in the machine tool coordinate system, the current work of each axis is detected by the respective position sensors (such as circular grat...
PUM
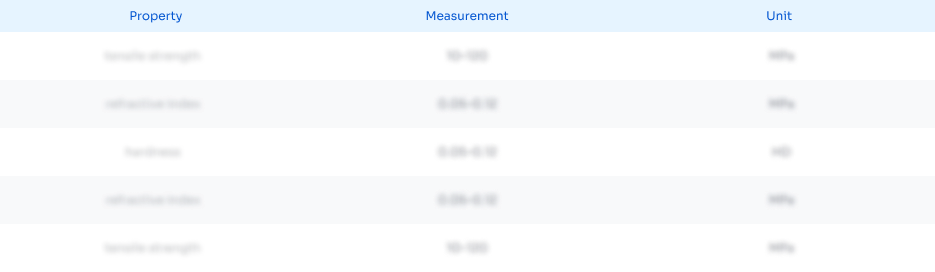
Abstract
Description
Claims
Application Information

- R&D
- Intellectual Property
- Life Sciences
- Materials
- Tech Scout
- Unparalleled Data Quality
- Higher Quality Content
- 60% Fewer Hallucinations
Browse by: Latest US Patents, China's latest patents, Technical Efficacy Thesaurus, Application Domain, Technology Topic, Popular Technical Reports.
© 2025 PatSnap. All rights reserved.Legal|Privacy policy|Modern Slavery Act Transparency Statement|Sitemap|About US| Contact US: help@patsnap.com