Waste oil regeneration method by phosphor salt flocculation, CO2 stirring and clay refining
A technology for refining white clay and regenerating waste oil, which is applied in the direction of lubricating composition, etc., can solve the problems of decreased physical and chemical properties of regenerated oil, difficult degradation and disposal of waste residue, increased dosage of additives, etc., achieves good flocculation effect, good coagulation effect, and prevents oxidation effect of action
- Summary
- Abstract
- Description
- Claims
- Application Information
AI Technical Summary
Problems solved by technology
Method used
Examples
Embodiment Construction
[0026] The present invention adopts "pretreatment water separation impurity-Na 3 PO 4 Flocculation and slag removal - heating dehydration - CO 2 Air-stirred clay decolorization and purification—plate and frame filter press—Na 3 PO 4 The alkaline washing-heating dehydration process regenerates waste compressor oil, waste hydraulic oil and waste refrigeration oil. That is, a phosphorus salt flocculates CO 2 Gas-stirred clay refining waste oil regeneration process. The regeneration rate of waste oil reaches more than 95%.
[0027] The invention is suitable for the regeneration application of waste oil in nitrogen fertilizer enterprises.
[0028] 1. Phosphate is used as coagulant for pretreatment water separation and oil removal residue. It is characterized by: preprocessing using Na 3 PO 4 The oil-water and oil-slag separation pretreatment has better agglomeration effect. Although the degree of processing is not deep each time, through Na 3 Po 4 After alkaline washing ...
PUM
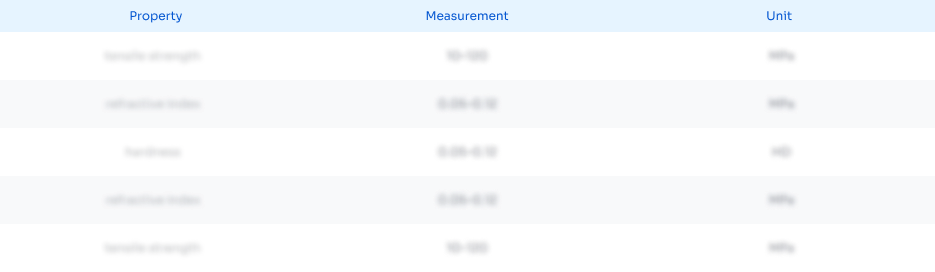
Abstract
Description
Claims
Application Information

- R&D
- Intellectual Property
- Life Sciences
- Materials
- Tech Scout
- Unparalleled Data Quality
- Higher Quality Content
- 60% Fewer Hallucinations
Browse by: Latest US Patents, China's latest patents, Technical Efficacy Thesaurus, Application Domain, Technology Topic, Popular Technical Reports.
© 2025 PatSnap. All rights reserved.Legal|Privacy policy|Modern Slavery Act Transparency Statement|Sitemap|About US| Contact US: help@patsnap.com