Organic silicon-acrylic ester copolymer emulsion and preparation and application thereof
A technology of acrylate and butyl acrylate, which is applied in the field of polymers, can solve the problems of stain resistance, poor water resistance and adhesion, paint adhesion, weather resistance, water resistance and stain resistance, and achieve anti-sticking and staining Improved performance, simple and easy construction method, and the effect of overcoming high energy consumption
- Summary
- Abstract
- Description
- Claims
- Application Information
AI Technical Summary
Problems solved by technology
Method used
Image
Examples
Embodiment 1
[0053] (1) Preparation of silicone-acrylate copolymer emulsion
[0054] Raw material ratio: by weight
[0055] 1 part silicone 3-glycidylpropyltrimethoxysilane, 1 part methyl methacrylate, 1 part butyl acrylate, 1 part methacrylic acid, 1 part beta-hydroxypropyl methacrylate, bicarbonate 1 part of sodium, 1 part of potassium persulfate, 1 part of compound emulsifier (0.5 part of non-ionic emulsifier Tween-20, 0.5 part of ionic emulsifier sodium lauryl sulfate), 1 part of deionized water.
[0056] Process: add deionized water, compound emulsifier and 0.2 parts of silicone, 0.2 parts of methyl methacrylate, 0.2 parts of butyl acrylate, 0.2 parts of methacrylic acid, 0.2 parts of -β-hydroxypropyl methacrylate, stirred and pre-emulsified at 20°C for 100 minutes; raised the temperature to 60°C, then added the remaining mixed monomers and potassium persulfate dropwise into the flask, stirred The polymerization reaction was carried out for 6 hours to obtain a blue-phase white silic...
Embodiment 2
[0064] (1) Silicone-acrylate copolymer emulsion is prepared from the following raw materials and processes:
[0065] Raw material ratio: by weight
[0066] 10 parts of silicone methacrylate propyltrimethoxysilane, 20 parts of methyl methacrylate, 30 parts of butyl acrylate, 10 parts of acrylic acid, 20 parts of β-hydroxypropyl methacrylate, 5 parts of sodium bicarbonate , 5 parts of ammonium persulfate, 5 parts of compound emulsifier (1 part of non-ionic emulsifier Tween-20, 4 parts of ionic sodium lauryl sulfate), 30 parts of deionized water.
[0067] Process: add deionized water, compound emulsifier and 0.5 parts of silicone, 1 part of methyl methacrylate, 1.5 parts of butyl acrylate into a four-necked flask equipped with an electric stirrer, a thermometer, a condenser and a dropping funnel , 0.5 parts of acrylic acid, 1 part of methacrylic acid-β-hydroxypropyl ester, stirred and pre-emulsified at 70°C for 20 minutes; raised the temperature to 85°C, then added the remaining...
Embodiment 3
[0075] (1) Silicone-acrylate copolymer emulsion is prepared from the following raw materials and processes:
[0076] Raw material ratio: by weight
[0077] 30 parts of silicone aminopropyl triethoxysilane, 50 parts of methyl methacrylate, 20 parts of butyl acrylate, 30 parts of fumaric acid, 20 parts of β-hydroxypropyl methacrylate, 8 parts of sodium bicarbonate , 8 parts of potassium persulfate, 8 parts of compound emulsifier (1 part of non-ionic emulsifier Tween-20, 7 parts of ionic sodium lauryl sulfate), 40 parts of deionized water.
[0078] Process: Add deionized water, compound emulsifier, 3 parts of silicone, 5 parts of methyl methacrylate, and 2 parts of butyl acrylate into a four-necked flask equipped with an electric stirrer, a thermometer, a condenser tube and a dropping funnel , 3 parts of fumaric acid, 2 parts of methacrylate-β-hydroxypropyl methacrylate, stirred and pre-emulsified at 60°C for 40 minutes; raised the temperature to 80°C, then added the remaining m...
PUM
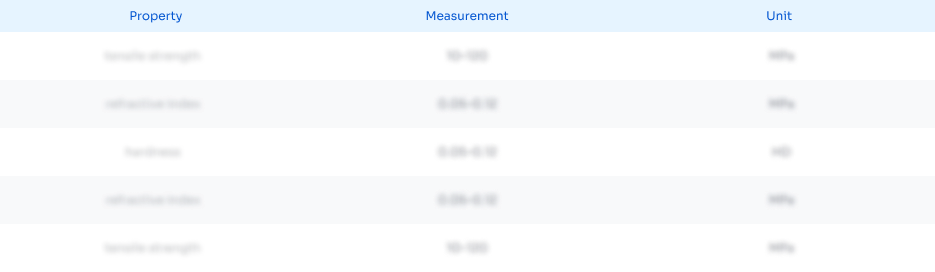
Abstract
Description
Claims
Application Information

- R&D
- Intellectual Property
- Life Sciences
- Materials
- Tech Scout
- Unparalleled Data Quality
- Higher Quality Content
- 60% Fewer Hallucinations
Browse by: Latest US Patents, China's latest patents, Technical Efficacy Thesaurus, Application Domain, Technology Topic, Popular Technical Reports.
© 2025 PatSnap. All rights reserved.Legal|Privacy policy|Modern Slavery Act Transparency Statement|Sitemap|About US| Contact US: help@patsnap.com