Composite damping shell of medium-small type motors
A compound damping and motor technology, applied in the direction of electric components, casing/cover/support, electrical components, etc., can solve the problems of increasing the weight and size of the motor, affecting the heat dissipation of the motor, discounting the vibration reduction effect, etc., and achieving weight and size Reduced effect
- Summary
- Abstract
- Description
- Claims
- Application Information
AI Technical Summary
Problems solved by technology
Method used
Image
Examples
Embodiment Construction
[0012] The present invention will be described in detail below in conjunction with the accompanying drawings.
[0013] Such as figure 1 , Shown in 2, the small and medium-sized motor composite damping housing of the present invention includes a pressure ring 1, a damping member 2, an iron core 3, an end plate 4, a bracket 5, a damping plate 6, and the like.
[0014] Both ends of the iron core 3 are provided with damping elements 2 respectively, and are fixedly connected to the bracket 5 through the pressure ring 1 and the end plate 4 respectively.
[0015] The iron core 3 is formed by laminating octagonal silicon steel sheets punched with axial ventilation holes; the damping part 2 is formed by punching composite damping material plates; the bracket 5 is formed by end rings welded on the end rings 45° direction and pasted with four ribs of the damping plate 6; and the damping part 2, the end plate 4, the iron core 3, the damping part 2, and the pressure ring 1 are stacked on ...
PUM
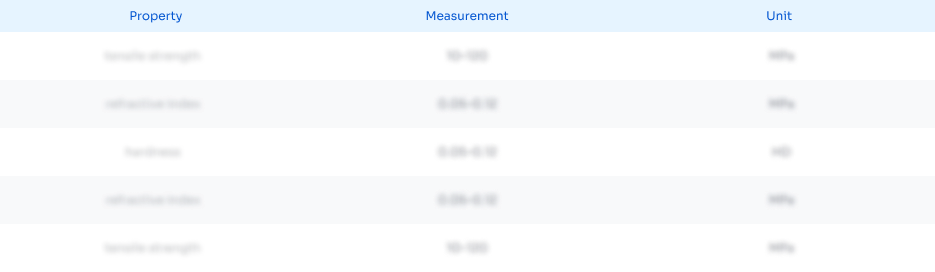
Abstract
Description
Claims
Application Information

- R&D Engineer
- R&D Manager
- IP Professional
- Industry Leading Data Capabilities
- Powerful AI technology
- Patent DNA Extraction
Browse by: Latest US Patents, China's latest patents, Technical Efficacy Thesaurus, Application Domain, Technology Topic, Popular Technical Reports.
© 2024 PatSnap. All rights reserved.Legal|Privacy policy|Modern Slavery Act Transparency Statement|Sitemap|About US| Contact US: help@patsnap.com