Method for dyeing conductive polyester fiber
A polyester fiber and dyeing method technology, applied in the field of dyeing, can solve the problems of the dye uptake rate of color difference, not high enough, less research on conductive fibers and fabric dyeing processes, etc., so as to retain the conductive effect, improve the dye uptake rate and color fastness. , reduce the effect of antistatic properties
- Summary
- Abstract
- Description
- Claims
- Application Information
AI Technical Summary
Problems solved by technology
Method used
Examples
Embodiment 1
[0018] A conductive polyester fiber dyeing process mainly includes the following steps: desizing→alkali weight reduction→dyeing→reduction cleaning.
[0019] In the desizing process, a sodium carbonate solution with a mass concentration of 0.2% is prepared, and detergent 209 is added to make the concentration 0.5%, the bath ratio is 1:30, the desizing temperature is 100 degrees, and after 60 minutes of desizing , take out the conductive fiber fabric and put it into the alkali weight reduction tank. The solution formula in the alkali reduction vat is: sodium hydroxide with a mass concentration of 3%, accelerator SN with a mass concentration of 0.1%; the liquor ratio is 1:30, the treatment temperature is 100 degrees, and after 30 minutes of treatment, it is put into the dyeing vat dyeing in. The solution ratio in the dyeing vat is: disperse blue SF-G with a mass concentration of 5%; ammonium sulfate with a mass concentration of 0.2%; dispersant NNO with a mass concentration of 0...
Embodiment 2
[0022] In the desizing process, a sodium carbonate solution with a mass concentration of 0.4% is prepared, and detergent 201 is added to make the concentration 0.8%, the bath ratio is 1:25, the desizing temperature is 90 degrees, and after 40 minutes of desizing , take out the conductive fiber fabric and put it into the alkali weight reduction tank. The formula of the solution in the alkali reduction vat is: sodium hydroxide with a mass concentration of 1%, accelerator SN with a mass concentration of 0.3%; the liquor ratio is 1:25, and the treatment temperature is 120 degrees. After 10 minutes of treatment, put it into the dyeing vat dyeing in. The solution ratio in the dyeing vat is: disperse blue SF-G with a mass concentration of 3%; disperse yellow UN-SE with a mass concentration of 2%, ammonium sulfate with a mass concentration of 0.4%; dispersant NNO with a mass concentration of 0.4%, The pH value of the solution is 4.0, and the dyeing temperature is 100 degrees. After 3...
Embodiment 3
[0024] In the desizing process, a sodium carbonate solution with a mass concentration of 0.3% is prepared, and detergent 209 is added to make the concentration 0.6%, the bath ratio is 1:25, the desizing temperature is 95 degrees, and after 50 minutes of desizing , take out the conductive fiber fabric and put it into the alkali weight reduction tank. The formula of the solution in the alkali reduction vat is: sodium hydroxide with a mass concentration of 5%, accelerator SN with a mass concentration of 0.2%; the bath ratio is 1:25, the treatment temperature is 70 degrees, and after 70 minutes of treatment, it is put into the dyeing vat dyeing in. The solution ratio in the dyeing vat is: disperse yellow UN-SE with a mass concentration of 10%, ammonium sulfate with a mass concentration of 0.1%; dispersant NNO with a mass concentration of 0.3%, the pH value of the solution is 4.5, and the dyeing temperature is 80 degrees. After 40 minutes of staining, enter the reduction wash. Th...
PUM
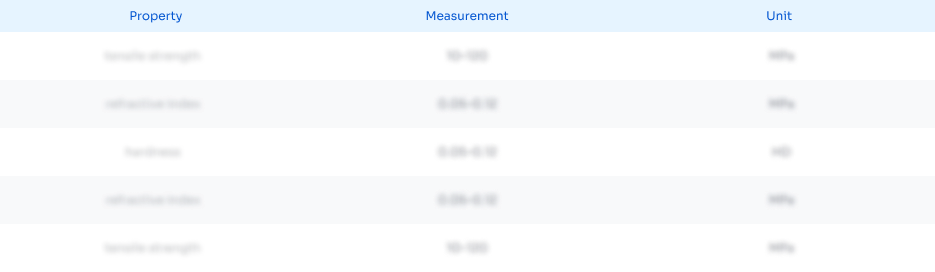
Abstract
Description
Claims
Application Information

- Generate Ideas
- Intellectual Property
- Life Sciences
- Materials
- Tech Scout
- Unparalleled Data Quality
- Higher Quality Content
- 60% Fewer Hallucinations
Browse by: Latest US Patents, China's latest patents, Technical Efficacy Thesaurus, Application Domain, Technology Topic, Popular Technical Reports.
© 2025 PatSnap. All rights reserved.Legal|Privacy policy|Modern Slavery Act Transparency Statement|Sitemap|About US| Contact US: help@patsnap.com