Method for preparing trifluorochloroethylene by halothane
A technology of chlorotrifluoroethylene and trifluoroethane, which is applied in the preparation of halogenated hydrocarbons, chemical instruments and methods, organic chemistry, etc., can solve the problem of high production cost of chlorotrifluoroethylene, and achieve low cost and high yield. Effect
- Summary
- Abstract
- Description
- Claims
- Application Information
AI Technical Summary
Problems solved by technology
Method used
Examples
Embodiment 1
[0015] exist A stainless steel tubular reactor is filled with a mixture of 3 kg of aluminum chloride, platinum chloride, palladium chloride and alumina, which contains 900 grams of aluminum chloride, 1980 grams of alumina, 90 grams of platinum chloride, and 30 grams of palladium chloride . The temperature of the reactor was raised to 350 °C, with N 2 The catalyst was activated for 10 hours and then cooled to 230°C. The feed rate of trifluoroethane was 1680 g / h, the feed rate of chlorine was 4970 g / h and the feed rate of hydrogen was 40 g / h. The product in the reactor is directly washed with water and alkali, then passed through a molecular sieve, condensed to collect chlorotrifluoroethylene and sampled for analysis. 2186.8 g of chlorotrifluoroethylene with a purity of 98.5% was obtained. Wherein the yield is 92.45%.
Embodiment 2
[0017] exist A stainless steel tubular reactor is filled with a mixture of 3 kg of aluminum chloride, platinum chloride, palladium chloride and alumina, which contains 477 grams of aluminum chloride, 2490 grams of alumina, 30 grams of platinum chloride, and 3 grams of palladium chloride . The temperature of the reactor was raised to 350 °C, with N 2 The catalyst was activated for 10 hours and then cooled to 300°C. The feed rate of trifluoroethane was 1680 g / h, the feed rate of chlorine was 4259 g / h and the feed rate of hydrogen was 55 g / h. The product in the reactor is directly washed with water and alkali, then passed through a molecular sieve, condensed to collect chlorotrifluoroethylene and sampled for analysis. 2185.3 g of chlorotrifluoroethylene with a purity of 98.7% was obtained. Wherein the yield is 92.57%.
Embodiment 3
[0019] exist A stainless steel tubular reactor is filled with a mixture of 3 kg of aluminum chloride, platinum chloride, palladium chloride and alumina, which contains 360 grams of aluminum chloride, 2550 grams of alumina, 60 grams of platinum chloride, and 30 grams of palladium chloride . The temperature of the reactor was raised to 350 °C, with N 2 The catalyst was activated for 10 hours and then cooled to 200°C. The feed rate of trifluoroethane was 1680 g / h, the feed rate of chlorine was 7100 g / h and the feed rate of hydrogen was 80 g / h. The product in the reactor is directly washed with water and alkali, then passed through a molecular sieve, condensed to collect chlorotrifluoroethylene and sampled for analysis. 2185.7 g of chlorotrifluoroethylene with a purity of 98.7% was obtained. Wherein the yield is 92.5%.
PUM
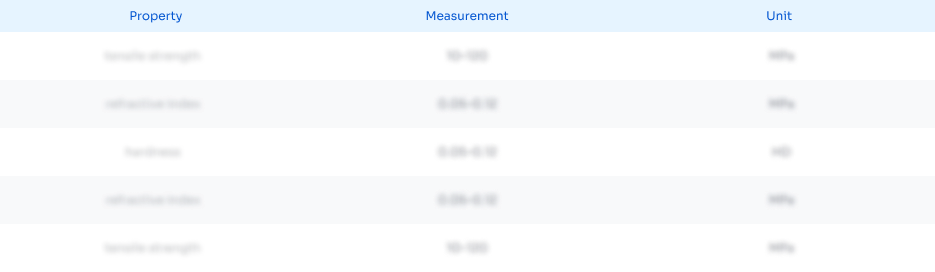
Abstract
Description
Claims
Application Information

- R&D
- Intellectual Property
- Life Sciences
- Materials
- Tech Scout
- Unparalleled Data Quality
- Higher Quality Content
- 60% Fewer Hallucinations
Browse by: Latest US Patents, China's latest patents, Technical Efficacy Thesaurus, Application Domain, Technology Topic, Popular Technical Reports.
© 2025 PatSnap. All rights reserved.Legal|Privacy policy|Modern Slavery Act Transparency Statement|Sitemap|About US| Contact US: help@patsnap.com