Method and equipment for recovering machine head material of plastic extruder/injection molding machine on site
A plastic extruder, on-site recycling technology, applied in the direction of plastic recycling and recycling technology, to achieve the effect of saving energy, maintaining the original performance, and reducing the workload of workers
- Summary
- Abstract
- Description
- Claims
- Application Information
AI Technical Summary
Problems solved by technology
Method used
Image
Examples
Embodiment Construction
[0019] A method for on-site recycling of plastic extruder / injection molding machine head material, comprising the following steps:
[0020] a) Heating and heat preservation: Send the head material just out of the extruder / injection molding machine directly into the heating insulation box to maintain or heat it to a high elastic state. The temperature of the head material in the high elastic state is usually 130-180°C ;The head material just out of the extruder / injection molding machine is in a high elastic state. The function of the heating insulation box is to ensure that the head material is still in a high elastic state before the pressing plate. Heating can be manually fed into the heating incubator, or it can be fed by automatic conveyor belt to save labor.
[0021] b) Press plate: Extrude the head material in a highly elastic state into a plate shape through a plate press machine;
[0022] c) Layering: Then the plate-shaped head material is sent to the layering machine ...
PUM
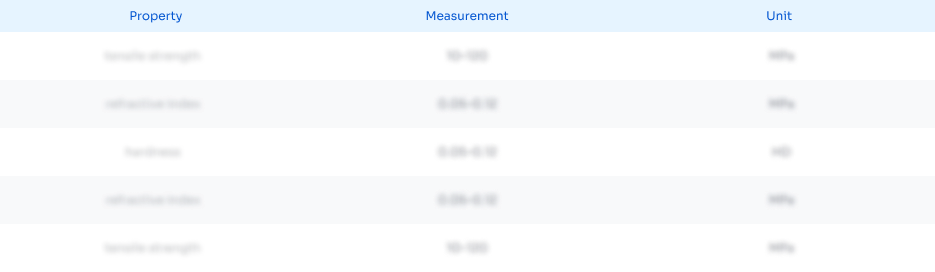
Abstract
Description
Claims
Application Information

- Generate Ideas
- Intellectual Property
- Life Sciences
- Materials
- Tech Scout
- Unparalleled Data Quality
- Higher Quality Content
- 60% Fewer Hallucinations
Browse by: Latest US Patents, China's latest patents, Technical Efficacy Thesaurus, Application Domain, Technology Topic, Popular Technical Reports.
© 2025 PatSnap. All rights reserved.Legal|Privacy policy|Modern Slavery Act Transparency Statement|Sitemap|About US| Contact US: help@patsnap.com