Final roller device and method for producing a magnesium strip in same
A technology of finishing rolling and magnesium strip, applied in metal rolling, manufacturing tools, metal rolling, etc., can solve the problem of long strip transmission distance, increase the installation cost of finishing rolling equipment and space requirements, increase the surface of the coiler strip, etc. question
- Summary
- Abstract
- Description
- Claims
- Application Information
AI Technical Summary
Problems solved by technology
Method used
Image
Examples
Embodiment Construction
[0028] According to the figures, the main components of the finishing rolling plant 10 consist of a roll stand 11 and two coilers 12, 13 which house the roll stand 11 between each other and together with the roll stand Set on a common floor plane 14. The figure also shows that the finishing rolling plant 10 is supplemented in this example by a preheating furnace 15 in the form of an elevated furnace arranged above and spaced from the floor level 14 . A reel supply device 17 with a horizontal conveyor 16 is located below this floor level 14, wherein two reel handling devices 18, 19 each featuring a vertical conveyor 20 are arranged below the coilers 12, 13 and assigned to the reel feeder.
[0029]According to the exemplary embodiment of the finishing rolling plant 10 shown in the figures, the two coilers 12, 13 and the roll stand 11 are provided with hood arrangements 21 and 22, respectively. In this example, the hood arrangements 21 of the coilers 12 , 13 each feature a coil...
PUM
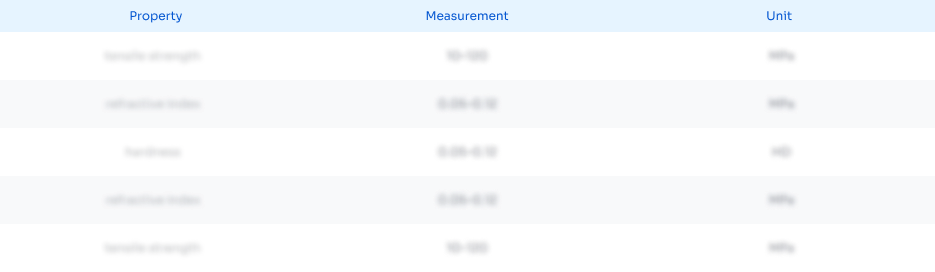
Abstract
Description
Claims
Application Information

- R&D
- Intellectual Property
- Life Sciences
- Materials
- Tech Scout
- Unparalleled Data Quality
- Higher Quality Content
- 60% Fewer Hallucinations
Browse by: Latest US Patents, China's latest patents, Technical Efficacy Thesaurus, Application Domain, Technology Topic, Popular Technical Reports.
© 2025 PatSnap. All rights reserved.Legal|Privacy policy|Modern Slavery Act Transparency Statement|Sitemap|About US| Contact US: help@patsnap.com