Comprehensive test system
A comprehensive testing and monitoring terminal technology, applied in the field of sensors, can solve the problems of manpower and financial resources loss, sensor sensitivity and accuracy changes, and acceleration cannot be achieved, and achieve the effect of saving financial resources
- Summary
- Abstract
- Description
- Claims
- Application Information
AI Technical Summary
Problems solved by technology
Method used
Image
Examples
Embodiment 1
[0028] The present invention will be further described in detail below in conjunction with the accompanying drawings and specific implementation.
[0029] figure 1 is a block diagram of a data acquisition system illustrating an integrated test system according to the present invention.
[0030] According to the comprehensive test system of the present invention, it includes sensors 11, . . . 1n, data acquisition device 2, field data monitoring terminal 3, network port 4, and remote client terminal 5.
[0031] Among them, the sensors 11,...1n mainly include vibrating wire sensors, resistance strain sensors, and acceleration sensors, which are used to detect the shaking amplitude and sinking displacement of the detected object, and transmit them to the data acquisition device 2 through signal cables. . For the resistance strain type full-bridge sensor and acceleration sensor signal, it is converted into a digital signal through amplification, linearization, gain correction, fi...
Embodiment 2
[0035] figure 2 It is a process flow diagram of the comprehensive testing system of the present invention.
[0036] The process flow chart of the comprehensive system of the present invention includes sensor detection, data collection and processing, engineering early warning, and client sending.
[0037] For the sensor detection part, it mainly completes the detection of whether the sensor is good or bad. The sensor is connected to the data acquisition part through a cable. After the connection and installation are completed, it is detected whether there is an overrange or damage. On the basis of ensuring that there are no failure problems, start data collection.
[0038]For the data processing and acquisition part, the resistance strain type acquisition module, the vibrating wire type acquisition module and the piezoelectric acquisition module are mainly installed. The vibrating wire acquisition module mainly processes the vibrating wire sensor connected on the cable, e...
Embodiment 3
[0044] image 3 It is a flow chart of the data collection and processing part of the present invention.
[0045] In the sensor detection section, each sensor 11....1n detects parameters such as acceleration, settlement, and swing of the building; then enters the data processing section, which collects signals from analog channels and digital channels. In this process, the vibrating wire sensor plays the role of a benchmark. Due to the relatively slow response speed, the long-term monitoring value is stable, and there is no long-term drift, so it is in a low-speed long-term working state. The drift of the building, and monitor the slow sinking and force of the building; the acceleration sensor has been in high-speed working state for a long time, and detects the acceleration of the building in real time, which is used to trigger and close the acquisition of the resistance strain type full bridge signal; the resistance strain type The sensor is in a standby state, and whether i...
PUM
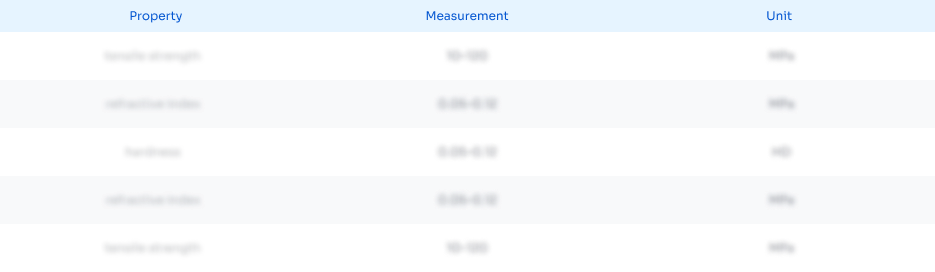
Abstract
Description
Claims
Application Information

- R&D Engineer
- R&D Manager
- IP Professional
- Industry Leading Data Capabilities
- Powerful AI technology
- Patent DNA Extraction
Browse by: Latest US Patents, China's latest patents, Technical Efficacy Thesaurus, Application Domain, Technology Topic, Popular Technical Reports.
© 2024 PatSnap. All rights reserved.Legal|Privacy policy|Modern Slavery Act Transparency Statement|Sitemap|About US| Contact US: help@patsnap.com