Crankshaft turning tool
A crankshaft and tooling technology, which is applied in the field of crankshaft turning tooling, can solve the problems of large number of eccentric shafts, large clamping diameter, and low work efficiency, so as to increase the amount of back cutting, increase the clamping force, and reduce the workload Effect
- Summary
- Abstract
- Description
- Claims
- Application Information
AI Technical Summary
Problems solved by technology
Method used
Image
Examples
Embodiment Construction
[0016] The present invention is described below in conjunction with specific embodiments.
[0017] Refer to attached figure 1 , The crankshaft turning tooling in this embodiment includes a three-jaw self-centering chuck 3, an indexing plate 4, a four-jaw single-action chuck 6, a front eccentric pad 5, a rear eccentric top block 2 and a counterweight 1.
[0018] The four-jaw single-action chuck is fixedly installed on the rotating shaft end of the horizontal lathe. The front eccentric pad 5 and the three-jaw self-centering chuck 3 are clamped on the four-jaw single-action chuck, wherein the front eccentric pad 5 is fixed between the four-jaw single-action chuck 6 and the three-jaw self-centering chuck 3 room, refer to the attached image 3 , there is a groove at the lower part of the front eccentric block Arc groove on the upper part The front eccentric pad is clamped on the lower jaw 10 of the four-jaw single-action chuck through the lower groove, and the arc groove on t...
PUM
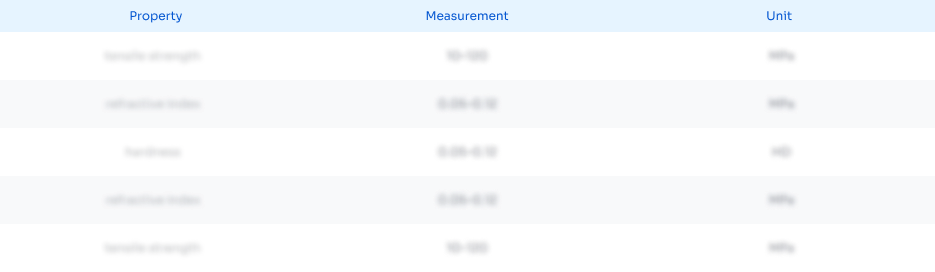
Abstract
Description
Claims
Application Information

- Generate Ideas
- Intellectual Property
- Life Sciences
- Materials
- Tech Scout
- Unparalleled Data Quality
- Higher Quality Content
- 60% Fewer Hallucinations
Browse by: Latest US Patents, China's latest patents, Technical Efficacy Thesaurus, Application Domain, Technology Topic, Popular Technical Reports.
© 2025 PatSnap. All rights reserved.Legal|Privacy policy|Modern Slavery Act Transparency Statement|Sitemap|About US| Contact US: help@patsnap.com