Straight line segment approximation node-based numerical control system contour error control method
A contour error, numerical control system technology, applied in the field of error compensation control, can solve the problems of large calculation error, unstable calculation, difficult to accurately predict the degree of lag, etc., and achieve the effects of good real-time performance, high calculation accuracy and simple calculation.
- Summary
- Abstract
- Description
- Claims
- Application Information
AI Technical Summary
Problems solved by technology
Method used
Image
Examples
Embodiment Construction
[0019] Combine below Figure 1~3 The present invention is described in further detail:
[0020] Step 1), after using the straight line segment to approach the command curve of the tool center trajectory of the machined part according to the equal error method, in each sampling period of the NC linear interpolation machining of the part, calculate the actual value of the current sampling period according to the position detection of the feed axis and the worktable. Tool position point coordinates, according to the actual tool position point and the approximation node when approaching the command curve of the tool center path with a straight line segment, calculate the shortest distance from the current actual tool position point to the command curve of the tool center path, that is, the contour error. Specific as figure 2 As shown, it is assumed that straight line segments AB, BC, etc. are used to approach the tool center trajectory command curve L of the part according to th...
PUM
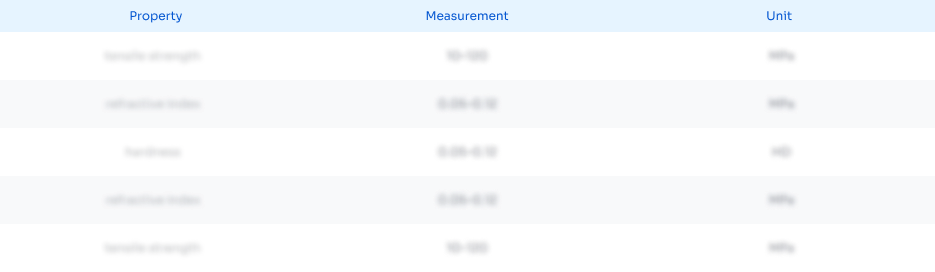
Abstract
Description
Claims
Application Information

- R&D
- Intellectual Property
- Life Sciences
- Materials
- Tech Scout
- Unparalleled Data Quality
- Higher Quality Content
- 60% Fewer Hallucinations
Browse by: Latest US Patents, China's latest patents, Technical Efficacy Thesaurus, Application Domain, Technology Topic, Popular Technical Reports.
© 2025 PatSnap. All rights reserved.Legal|Privacy policy|Modern Slavery Act Transparency Statement|Sitemap|About US| Contact US: help@patsnap.com