Symmetrical multi-cavity discharging technology
A multi-cavity and process technology, applied in the field of symmetrical multi-cavity discharge technology, can solve problems such as affecting the surface flatness and cross-section quality of the workpiece, inability to align accurately, and process waste products, and achieve good workpiece cross-section quality and flatness. , Improve the genuine rate, improve the effect of flatness
- Summary
- Abstract
- Description
- Claims
- Application Information
AI Technical Summary
Problems solved by technology
Method used
Image
Examples
Embodiment Construction
[0023] The present invention will now be further described in detail in conjunction with the accompanying drawings and embodiments. These drawings are all simplified schematic diagrams, only illustrating the basic structure of the present invention in a schematic manner, so it only shows the composition related to the present invention.
[0024] Such as figure 1 , figure 2 As shown, in the symmetrical multi-cavity discharge process of the present invention, the working object of the discharge process is a flat strip, and the formed product is an oblate ring columnar workpiece punched from the strip. The process The steps include: cutting, punching, chamfering, half cutting, shaping and blanking. Specifically, the first step of cutting is to pre-cut the material tape, determine the processing position of each workpiece, and cut the positions of two adjacent workpieces along the processing direction of the material tape to leave a gap. Further, cut out the shape of the outer ...
PUM
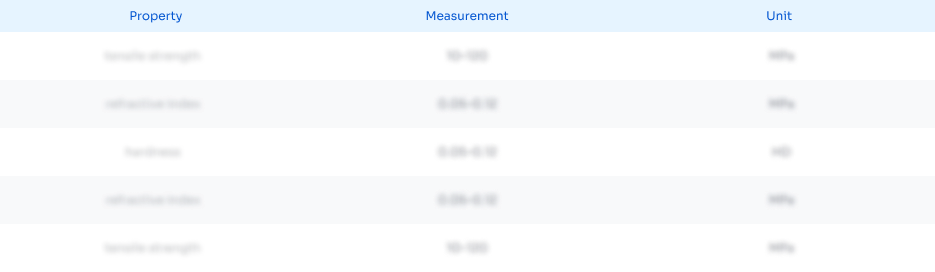
Abstract
Description
Claims
Application Information

- R&D
- Intellectual Property
- Life Sciences
- Materials
- Tech Scout
- Unparalleled Data Quality
- Higher Quality Content
- 60% Fewer Hallucinations
Browse by: Latest US Patents, China's latest patents, Technical Efficacy Thesaurus, Application Domain, Technology Topic, Popular Technical Reports.
© 2025 PatSnap. All rights reserved.Legal|Privacy policy|Modern Slavery Act Transparency Statement|Sitemap|About US| Contact US: help@patsnap.com