Novel bismuth smelting separation method
A new method, the technology of bismuth oxide, is applied in the direction of elements such as selenium/tellurium, which can solve the problems of low recovery rate, high cost, and environmental pollution, and achieve the effects of increasing bismuth content, reducing energy consumption, and improving purity
- Summary
- Abstract
- Description
- Claims
- Application Information
AI Technical Summary
Problems solved by technology
Method used
Image
Examples
Embodiment 1
[0013] 8 tons of bismuth compound, its composition is: bismuth 56.40wt%, tellurium 1.51wt%, moisture 35.22wt%.
[0014] (1) Add the bismuth compound to the stirred reactor, add tap water according to the solid-to-liquid mass ratio of 1:1, start the machine and stir until the bismuth compound becomes a slurry, and add it to the reactor according to the ratio of mass ratio bismuth: sodium hydroxide = 1:0.5 Solid sodium hydroxide, after adding alkali, control the reaction temperature at 90-95°C, stir and react for 1 hour, so that bismuth is converted into bismuth oxide, tellurium is dissolved into the alkali solution, and then bismuth oxide and tellurium-containing alkali solution are separated by pressure filtration Obtain bismuth oxide and tellurium lye respectively, and wash the bismuth oxide with water.
[0015] (2) The main components of the bismuth oxide obtained by adding alkali are: bismuth 78.45wt%, tellurium 0.10wt%, water 13.41wt%. Bismuth oxide is uniformly mixed acc...
Embodiment 2
[0018] 10 tons of bismuth compound, its composition is: bismuth 54.64wt%, tellurium 1.43wt%, water 30.25wt%.
[0019] (1) Add the bismuth compound to the stirred reactor, add tap water according to the solid-to-liquid mass ratio of 1:1.5, start the machine and stir until the bismuth compound becomes a slurry, and add it to the reactor according to the mass ratio of bismuth: sodium hydroxide = 1:0.6 Solid sodium hydroxide, after adding alkali, control the reaction temperature at 90-95°C, stir and react for 1.4 hours to convert bismuth into bismuth oxide, tellurium dissolves into the alkali solution, and then separate the bismuth oxide and tellurium-containing alkali solution through pressure filtration Obtain bismuth oxide and tellurium lye respectively, and wash the bismuth oxide with water.
[0020] (2) The main components of the bismuth oxide obtained by adding alkali are: bismuth 77.13wt%, tellurium 0.10wt%, water 14.81wt%. Bismuth oxide is uniformly mixed according to the...
Embodiment 3
[0023] 9.5 tons of bismuth compound, its composition is: bismuth 53.10wt%, tellurium 1.02wt%, water 27.32wt%.
[0024] (1) Add the bismuth compound to the stirred reactor, add tap water according to the solid-to-liquid mass ratio of 1:2, start the machine and stir until the bismuth compound becomes a slurry, and add it to the reactor according to the mass ratio of bismuth: sodium hydroxide = 1:0.8 Solid sodium hydroxide, after adding alkali, control the reaction temperature at 90-95°C, and stir for 2 hours to convert bismuth into bismuth oxide, tellurium dissolves into the alkali solution, and then separate bismuth oxide and tellurium-containing alkali solution through pressure filtration Obtain bismuth oxide and tellurium lye respectively, and wash the bismuth oxide with water.
[0025] (2) The main components of the bismuth oxide obtained by adding alkali are: bismuth 75.69wt%, tellurium 0.08wt%, water 14.85wt%. Bismuth oxide is uniformly mixed according to the mass ratio o...
PUM
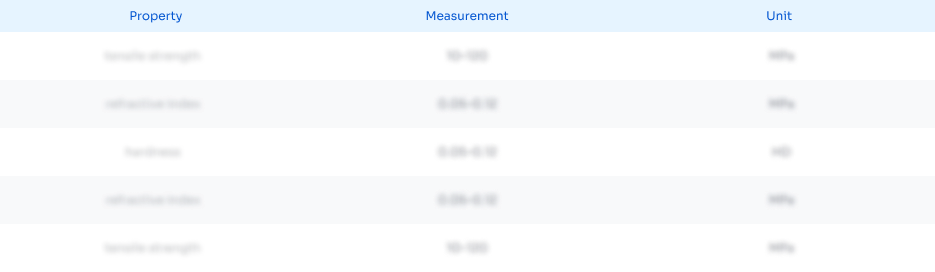
Abstract
Description
Claims
Application Information

- R&D
- Intellectual Property
- Life Sciences
- Materials
- Tech Scout
- Unparalleled Data Quality
- Higher Quality Content
- 60% Fewer Hallucinations
Browse by: Latest US Patents, China's latest patents, Technical Efficacy Thesaurus, Application Domain, Technology Topic, Popular Technical Reports.
© 2025 PatSnap. All rights reserved.Legal|Privacy policy|Modern Slavery Act Transparency Statement|Sitemap|About US| Contact US: help@patsnap.com