Polyphenylether cable compound for adjusting hardness and preparation method thereof
A polyphenylene ether and cable material technology, applied in the direction of insulated cables, cables, circuits, etc., can solve problems such as hindering application and poor processing performance, and achieve the effect of reducing dosage, reducing hardness and smooth appearance
- Summary
- Abstract
- Description
- Claims
- Application Information
AI Technical Summary
Problems solved by technology
Method used
Image
Examples
Embodiment 1
[0039] Weigh the material according to the following parts by mass: 20 parts by mass of PPE resin, 35 parts by mass of SEBS, 15 parts by mass of PP, 20 parts by mass of TPP, Mg(OH) 2 10 parts by mass, 0.1 part by mass of antioxidant 1010, 0.1 part by mass of lubricant, and 0.2 parts by mass of antioxidant 168 were added to the mixer for pre-mixing, and the mixing temperature was 70 ° C. The rotating speed of the mixer is 100 rpm, and the mixing time is 5 minutes. The pre-mixed material is fed into a twin-screw extruder for extrusion granulation. During extrusion, the processing temperature of each section of the twin-screw extruder is set to 220°C for the first section, 240°C for the second section, 260°C for the third section, 260°C for the fourth section, 260°C for the fifth section, and 260°C for the sixth section. , The seventh section is 260°C, the eighth section is 260°C, the ninth section is 260°C, the die head temperature is 255°C, the aspect ratio of the twin-screw i...
Embodiment 2
[0042] Weigh the material according to the following parts by mass: 20 parts by mass of PPE resin, 35 parts by mass of SEBS, 15 parts by mass of PP, 20 parts by mass of TPP, Mg(OH) 2 10 parts by mass, 25 parts by mass of plasticizer, 0.1 part by mass of lubricant, 0.1 part by mass of antioxidant 1010, and 0.2 parts by mass of antioxidant 168 were added and mixed in turn Machine pre-mixing, the mixing temperature is 70°C, the speed of the mixer is 100 rpm, and the mixing time is 5 minutes.
[0043] The pre-mixed material is fed into a twin-screw extruder for extrusion granulation. During extrusion, the processing temperature of each section of the twin-screw extruder is set to 220°C for the first section, 240°C for the second section, 260°C for the third section, 260°C for the fourth section, 260°C for the fifth section, and 260°C for the sixth section. , The seventh section is 260°C, the eighth section is 260°C, the ninth section is 260°C, the die head temperature is 255°C, t...
Embodiment 3
[0046] Weigh the following substances in parts by mass: 30 parts by mass of PPE resin, 40 parts by mass of SBS, 20 parts by mass of PP, 25 parts by mass of TPP, Mg(OH) 210 parts by mass, 60 parts by mass of plasticizer, 0.3 parts by mass of lubricant, 0.8 parts by mass of antioxidant 1010, and 0.2 parts by mass of antioxidant 168 were added and mixed in turn Machine pre-mixing, the mixing temperature is 80°C, the speed of the mixer is 800 rpm, and the mixing time is 6 minutes.
[0047] The pre-mixed material is fed into a twin-screw extruder for extrusion granulation. During extrusion, the processing temperature of each section of the twin-screw extruder is set to 220°C for the first section, 240°C for the second section, 260°C for the third section, 260°C for the fourth section, 260°C for the fifth section, and 260°C for the sixth section. , The seventh section is 260°C, the eighth section is 260°C, the ninth section is 300°C, the die temperature is 255°C, the twin-screw len...
PUM
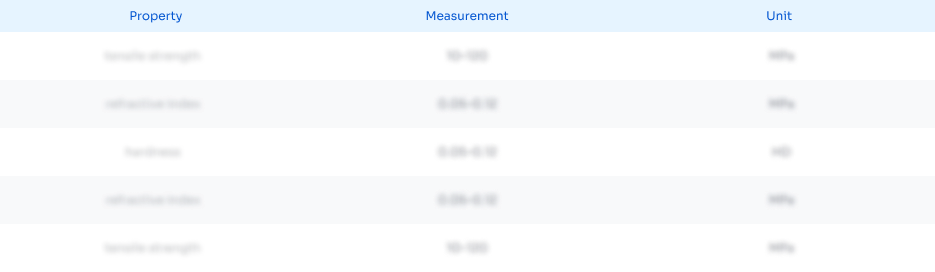
Abstract
Description
Claims
Application Information

- R&D
- Intellectual Property
- Life Sciences
- Materials
- Tech Scout
- Unparalleled Data Quality
- Higher Quality Content
- 60% Fewer Hallucinations
Browse by: Latest US Patents, China's latest patents, Technical Efficacy Thesaurus, Application Domain, Technology Topic, Popular Technical Reports.
© 2025 PatSnap. All rights reserved.Legal|Privacy policy|Modern Slavery Act Transparency Statement|Sitemap|About US| Contact US: help@patsnap.com