Regenerated terylene filament and preparation method thereof
A polyester filament and base material technology, applied in the field of synthetic fibers and its preparation, can solve the problems of no original key technology, no industrial production reports, etc., achieve good mechanical properties and wearing comfort, avoid exhaustion, and improve solution The effect of aggregation rate
- Summary
- Abstract
- Description
- Claims
- Application Information
AI Technical Summary
Problems solved by technology
Method used
Image
Examples
Embodiment 1
[0033] in such as figure 1 In the reaction kettle 1 shown, put 10kg of polyester waste silk, 1kg of ethylene glycol, and zinc acetate accounting for 3‰ of polyester waste, and depolymerize at 220°C for 3 hours under a pressure of 1kg. reaction;
[0034] After the reaction is over, lower the temperature of the ethylene glycol depolymerization product to 130-170°C, pass the depolymerization product through a 30-100-mesh filter to remove unreacted waste PET, and then pass the depolymerization product through an activated carbon adsorption column for further adsorption Colored impurities or higher molecular weight polymers, further purify the depolymerization products. Finally, the depolymerization product is pushed into the reactor 2;
[0035] First adjust the temperature of the second reactor to 280° C., and carry out pre-condensation by vacuuming for 30 minutes. When the vacuum degree reaches below 100 Pa, the polycondensation reaction is carried out for 2 hours. After the p...
Embodiment 2
[0037] Drop into the 3rd component BHET of 1kg in the first reactor, and add the same amount of waste silk, ethylene glycol, and catalyzer as in Example 1 to react under the same conditions;
[0038] After the reaction finishes, adopt the same steps as in Example 1 to push the depolymerization product into the second reactor
[0039] First adjust the temperature of the second reactor to 280° C., and carry out pre-condensation by vacuuming for 30 minutes. When the vacuum degree reaches below 100 Pa, the polycondensation reaction is carried out for 3 hours. After the polycondensation reaction, pelletizing, drying, and spinning are carried out to obtain recycled polyester filaments.
Embodiment 3
[0041] in the present invention figure 1 In the reaction kettle 1 shown, put 20kg of polyester waste silk, 40kg of ethylene glycol, and ethylene glycol antimony accounting for 0.1‰ of polyester waste, under a pressure of 4kg, heat preservation at 260°C, and hold pressure for 3 hours. depolymerization reaction;
[0042] Adopt the same step as Example 1 to push the depolymerization product into the second reaction kettle after the reaction finishes;
[0043] Add 6g of ethylene glycol antimony catalyst and 4g of trimethyl phosphate into the second reaction kettle, and adjust the temperature to 280°C, vacuumize for pre-condensation for 1h, and carry out polycondensation reaction when the vacuum reaches below 100Pa , The reaction time is 1.5h. After the polycondensation reaction, pelletizing, drying, and spinning are carried out to obtain recycled polyester filaments.
PUM
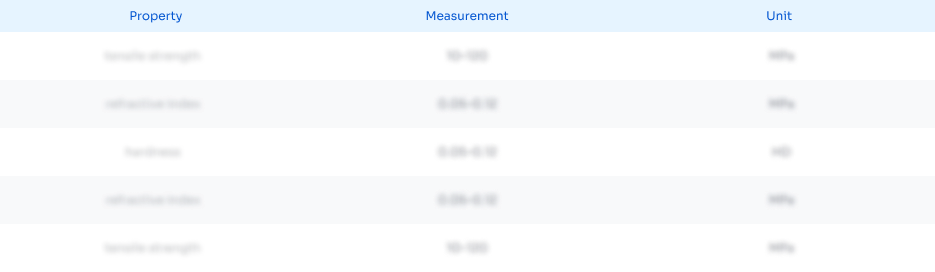
Abstract
Description
Claims
Application Information

- Generate Ideas
- Intellectual Property
- Life Sciences
- Materials
- Tech Scout
- Unparalleled Data Quality
- Higher Quality Content
- 60% Fewer Hallucinations
Browse by: Latest US Patents, China's latest patents, Technical Efficacy Thesaurus, Application Domain, Technology Topic, Popular Technical Reports.
© 2025 PatSnap. All rights reserved.Legal|Privacy policy|Modern Slavery Act Transparency Statement|Sitemap|About US| Contact US: help@patsnap.com