Production method of attapulgite loaded hydroxyapatite composite defluorination filter bulb
A technology of hydroxyapatite and attapulgite, which is applied in the direction of ion exchange water/sewage treatment, adsorption water/sewage treatment, etc., can solve the problems of mixed calcium hydrogen phosphate, affecting the defluoridation capacity of the product, and achieve high yield and purity High, conducive to large-scale production and popularization and utilization, high effect of fluorine removal capacity
- Summary
- Abstract
- Description
- Claims
- Application Information
AI Technical Summary
Problems solved by technology
Method used
Examples
Embodiment 1
[0025] 1. Add 500L water into the reactor and heat to 75°C;
[0026] 2. Add 1.5 kg of glacial acetic acid and stir evenly;
[0027] 3. Weigh 125Kg of calcium hydroxide, add it to the reaction kettle, and stir for 4 minutes;
[0028] 4. Add 105kg of phosphoric acid into 315kg of water and stir evenly to form a solution;
[0029] 5. Add the above-mentioned phosphoric acid solution dropwise into the reactor, and control the dropping rate to be 12kg / min;
[0030] 6. React at a temperature of 75°C for 2.5 hours;
[0031] 7. Add 70kg attapulgite, stir evenly, and react for 1 hour at a temperature of 75°C;
[0032] 8. Take out the product, perform dehydration, washing, drying, and crushing to obtain attapulgite-loaded hydroxyapatite powder;
[0033] 9. Put the attapulgite-loaded hydroxyapatite powder into the ball forming machine, spray the sodium carboxymethyl cellulose binder with a mass percentage of 1%, and make the powder into small balls with a diameter of 0.5-1.5 mm. ball...
Embodiment 2
[0036] 1. Add 500L water into the reactor and heat to 75°C;
[0037] 2. Add 2kg of glacial acetic acid and stir evenly;
[0038] 3. Weigh 125Kg of calcium hydroxide, add it to the reaction kettle, and stir for 5 minutes;
[0039] 4. Add 100kg of phosphoric acid into 300kg of water and stir evenly to form a solution;
[0040] 5. Add the above-mentioned phosphoric acid solution dropwise into the reactor, and control the dropping rate to be 10kg / min;
[0041] 6. React at a temperature of 75°C for 2.5 hours;
[0042] 7. Add 63kg attapulgite, stir evenly, and react for 1 hour at a temperature of 75°C;
[0043] 8. Take out the product, perform dehydration, washing, drying, and crushing to obtain attapulgite-loaded hydroxyapatite powder;
[0044] 9. Put the attapulgite-loaded hydroxyapatite powder into the ball forming machine, spray the hydroxyethyl cellulose binder with a mass percentage of 1%, and make the powder into small balls with a diameter of 0.5-1.5mm ;
[0045] 10. T...
Embodiment 3
[0047] 1. Add 500L water into the reactor and heat to 80°C;
[0048] 2. Add 1kg of glacial acetic acid and stir evenly;
[0049] 3. Weigh 125Kg of calcium hydroxide, add it to the reaction kettle, and stir for 3 minutes;
[0050] 4. Add 110kg of phosphoric acid into 330kg of water and stir evenly to form a solution;
[0051] 5. Add the above-mentioned phosphoric acid solution dropwise into the reactor, and control the dropping rate to be 15kg / min;
[0052] 6. React for 2.5 hours at 80°C;
[0053] 7. Add 75kg attapulgite, stir evenly, and react for 1 hour at a temperature of 80°C;
[0054] 8. Take out the product, perform dehydration, washing, drying, and crushing to obtain attapulgite-loaded hydroxyapatite powder;
[0055] 9. Put the attapulgite-loaded hydroxyapatite powder into the ball forming machine, spray the sodium carboxymethyl cellulose binder with a mass percentage of 1.5%, and make the powder into small balls with a diameter of 0.5-1.5 mm. ball;
[0056] 10. Ta...
PUM
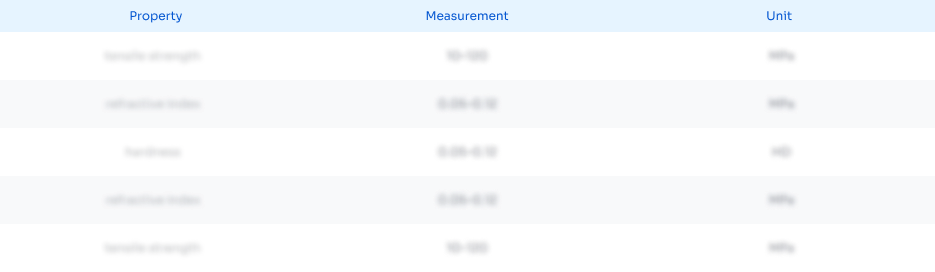
Abstract
Description
Claims
Application Information

- Generate Ideas
- Intellectual Property
- Life Sciences
- Materials
- Tech Scout
- Unparalleled Data Quality
- Higher Quality Content
- 60% Fewer Hallucinations
Browse by: Latest US Patents, China's latest patents, Technical Efficacy Thesaurus, Application Domain, Technology Topic, Popular Technical Reports.
© 2025 PatSnap. All rights reserved.Legal|Privacy policy|Modern Slavery Act Transparency Statement|Sitemap|About US| Contact US: help@patsnap.com