Curing method of novel catalyst
A catalyst and vulcanization reaction technology, applied in chemical instruments and methods, chemical industry, ammonia preparation/separation, etc., can solve the problems of low resource security, long parking time, waste of new catalyst production, etc., to prolong equipment life, Energy saving and energy saving effects
- Summary
- Abstract
- Description
- Claims
- Application Information
AI Technical Summary
Problems solved by technology
Method used
Examples
Embodiment Construction
[0007] The vulcanization method of a kind of new catalyst of the present invention is: add a heat exchanger between the blower fan and the heater of the converter system, add a water cooler between the heat exchanger and the blower fan, make the blower fan, heat exchanger, The heater, the converter and the water cooler form a closed circulation system; a new catalyst is installed in the converter; the fan is turned on, and the semi-water gas delivered by the fan enters the heat exchanger to exchange heat with the high-temperature semi-water gas reacted in the converter. Then it enters the heating furnace for further heating, and then enters the converter furnace for catalytic vulcanization reaction. After the reaction, it enters the heat exchanger to exchange heat with the semi-water gas newly transported by the fan to reduce the temperature. After further reducing the temperature through the water cooler, it re-enters the system circulation through the fan use.
PUM
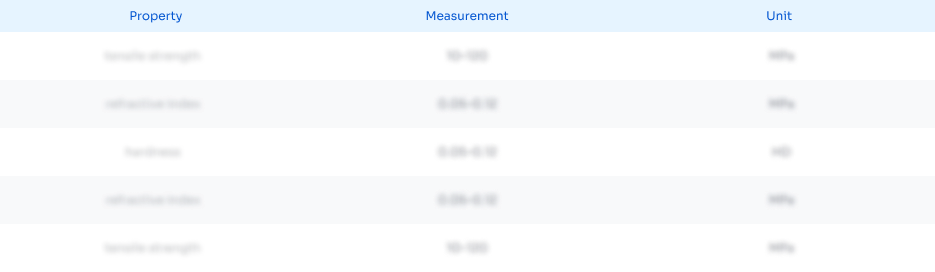
Abstract
Description
Claims
Application Information

- R&D
- Intellectual Property
- Life Sciences
- Materials
- Tech Scout
- Unparalleled Data Quality
- Higher Quality Content
- 60% Fewer Hallucinations
Browse by: Latest US Patents, China's latest patents, Technical Efficacy Thesaurus, Application Domain, Technology Topic, Popular Technical Reports.
© 2025 PatSnap. All rights reserved.Legal|Privacy policy|Modern Slavery Act Transparency Statement|Sitemap|About US| Contact US: help@patsnap.com