Method for manufacturing printed circuit board (PCB) with step-shaped grooves
A technology of PCB boards and manufacturing methods, which is applied in the fields of printed circuit manufacturing, electrical components, printed circuits, etc., can solve the problems of complex manufacturing process, long cycle, unfavorable batch production, etc., and achieve the effect of high efficiency and simple manufacturing process
- Summary
- Abstract
- Description
- Claims
- Application Information
AI Technical Summary
Problems solved by technology
Method used
Image
Examples
Embodiment Construction
[0022] Such as Figure 1 to Figure 7 Shown, the manufacturing method of the PCB board of tool stepped groove of the present invention, comprises the following steps:
[0023] Step 1: Provide a core board 10 and a prepreg 20, and make an inner layer pattern on the core board 10, one of the core boards 10 has a target layer 11 corresponding to the bottom of the stepped groove 13 to be made, in the A target copper layer 111 is made on the target layer 11 corresponding to the position of the stepped groove 13 to be made, and a peripheral copper layer 112 and a wire 113 are made on the target layer 11 on the periphery of the target copper layer 111. Layer 112 is spaced from the target copper layer 111 and connected to the target copper layer 111 by wire 113, the structure of the target layer 11 is as follows Figure 6 shown;
[0024] Step 2: Press the core board 10 and the prepreg 20 according to a predetermined stacking sequence to form a laminated board. The structure of the la...
PUM
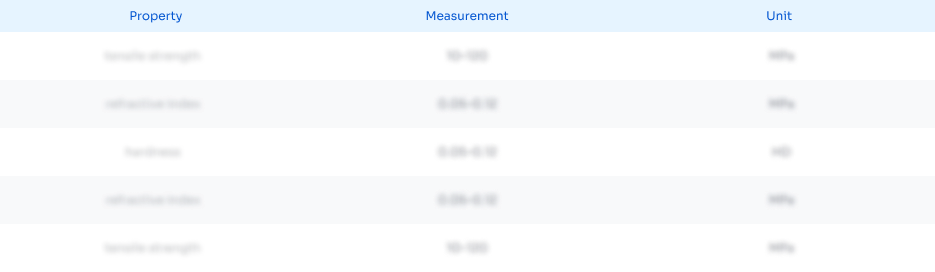
Abstract
Description
Claims
Application Information

- Generate Ideas
- Intellectual Property
- Life Sciences
- Materials
- Tech Scout
- Unparalleled Data Quality
- Higher Quality Content
- 60% Fewer Hallucinations
Browse by: Latest US Patents, China's latest patents, Technical Efficacy Thesaurus, Application Domain, Technology Topic, Popular Technical Reports.
© 2025 PatSnap. All rights reserved.Legal|Privacy policy|Modern Slavery Act Transparency Statement|Sitemap|About US| Contact US: help@patsnap.com