Preparation method for anti-flaming bamboo floor
A bamboo floor, flame retardant technology, applied in the direction of floors, buildings, building structures, etc., can solve problems such as fire hazards, reduce free formaldehyde content, good loss resistance, and good flame retardant performance. Effect
- Summary
- Abstract
- Description
- Claims
- Application Information
AI Technical Summary
Problems solved by technology
Method used
Image
Examples
Embodiment 1
[0016] Embodiment 1: a kind of fire-retardant bamboo floor preparation method, it comprises the following steps successively
[0017] (1) The original bamboo warp is cut into pieces and sawed to obtain a plain board;
[0018] (2) Carbonization treatment, put the bamboo chips into a high-pressure treatment tank, then introduce high-pressure saturated steam into the tank, raise the pressure to 0.2MPa, keep the heat for 3 hours, and finally release the pressure. water out again;
[0019] (3) Drying, place the base plate in a drying oven to control the temperature in the drying oven to 150°C, the humidity to 75%, and the drying time to 2 hours, so that the moisture content of the base plate is adjusted to 8%;
[0020] (4) Flame retardant treatment: vacuum pressure impregnation method, vacuum degree 80kPa, vacuum time 1.5h, impregnation pressure 0.5MPa, impregnation time 2h; flame retardant consists of the following raw materials with the following components and corresponding per...
Embodiment 2
[0024] Embodiment 2: a kind of fire-retardant bamboo floor preparation method, it comprises the following steps successively
[0025] (1) The original bamboo warp is cut into pieces and sawed to obtain a plain board;
[0026] (2) Carbonization treatment, put the bamboo chips into a high-pressure treatment tank, then introduce high-pressure saturated steam into the tank, raise the pressure to 0.3MPa, keep the heat for 4 hours, and finally release the pressure. water out again;
[0027] (3) Drying, place the base plate in a drying oven to control the temperature in the drying oven to 160°C, the humidity to 80%, and the drying time to 3 hours, so that the moisture content of the base plate is adjusted to 5%;
[0028] (4) Flame retardant treatment: Vacuum pressurized impregnation method, vacuum degree 87kPa, vacuum time 2h, impregnation pressure 0.6MPa, impregnation time 3h; flame retardant is mixed with the following components and corresponding percentages of raw materials be ...
Embodiment 3
[0032] Embodiment 3: a kind of flame-retardant bamboo floor preparation method, it comprises the following steps successively
[0033] (1) The original bamboo warp is cut into pieces and sawed to obtain a plain board;
[0034] (2) Carbonization treatment, put the bamboo slices into the high-pressure treatment tank, then introduce high-pressure saturated steam into the tank, raise the pressure to 0.25MPa, keep the heat for 3.5 hours, and finally release the pressure. water out again;
[0035] (3) Drying, place the base plate in a drying oven to control the temperature in the drying oven to 155°C, the humidity to 77%, and the drying time to 2.5 hours, so that the moisture content of the base plate is adjusted to 6%;
[0036] (4) Flame retardant treatment: adopt vacuum pressure impregnation method, vacuum degree 85kPa, vacuum time 1.7h, impregnation pressure 0.5MPa, impregnation time 2.5h; flame retardant consists of components and corresponding percentages as follows Raw mater...
PUM
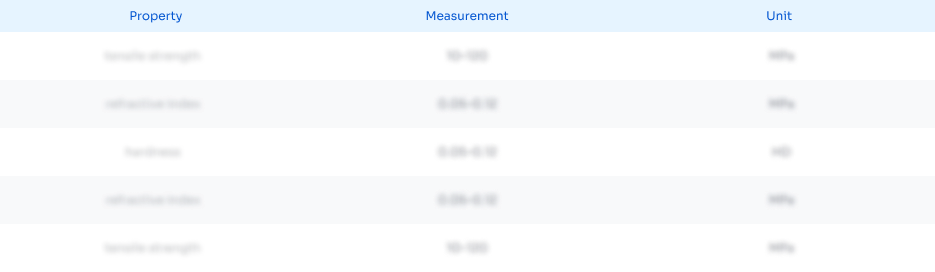
Abstract
Description
Claims
Application Information

- R&D
- Intellectual Property
- Life Sciences
- Materials
- Tech Scout
- Unparalleled Data Quality
- Higher Quality Content
- 60% Fewer Hallucinations
Browse by: Latest US Patents, China's latest patents, Technical Efficacy Thesaurus, Application Domain, Technology Topic, Popular Technical Reports.
© 2025 PatSnap. All rights reserved.Legal|Privacy policy|Modern Slavery Act Transparency Statement|Sitemap|About US| Contact US: help@patsnap.com