Method for forging steering knuckle
A steering knuckle and pre-forging technology is applied in the field of steering knuckle forging, which can solve the problems of inability to fill the forgings, difficult processing and quality, and achieve the effects of good forming performance, cutting material and low equipment requirements.
- Summary
- Abstract
- Description
- Claims
- Application Information
AI Technical Summary
Problems solved by technology
Method used
Image
Examples
Embodiment Construction
[0014] Below in conjunction with accompanying drawing and embodiment, further elaborate the present invention. In the following detailed description, certain exemplary embodiments of the invention are described by way of illustration only. Needless to say, those skilled in the art would realize that the described embodiments can be modified in various different ways, all without departing from the spirit and scope of the present invention. Accordingly, the drawings and description are illustrative in nature and not intended to limit the scope of the claims.
[0015] Steering knuckle forging method, including process blanking, heating, billet making, pre-forging, final forging, edge trimming, and shaping, heating the cylindrical blank after blanking, and the cylindrical blank after heating includes billet making, pre-forging, After final forging, trimming and shaping, the steering knuckle is made,
[0016] First, round steel is used as the raw material to cut into a cylindric...
PUM
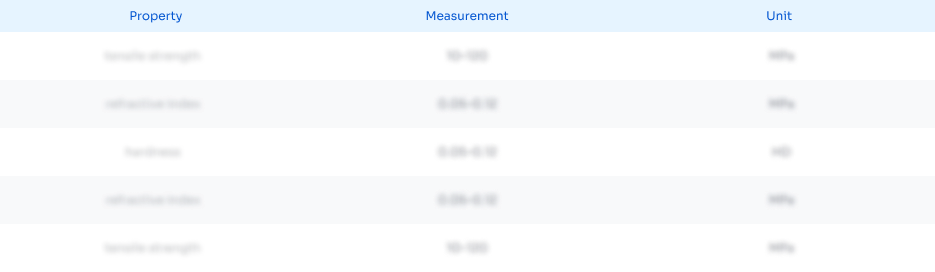
Abstract
Description
Claims
Application Information

- Generate Ideas
- Intellectual Property
- Life Sciences
- Materials
- Tech Scout
- Unparalleled Data Quality
- Higher Quality Content
- 60% Fewer Hallucinations
Browse by: Latest US Patents, China's latest patents, Technical Efficacy Thesaurus, Application Domain, Technology Topic, Popular Technical Reports.
© 2025 PatSnap. All rights reserved.Legal|Privacy policy|Modern Slavery Act Transparency Statement|Sitemap|About US| Contact US: help@patsnap.com