Internal foaming rubber of dual density Goodyear outsole and preparation method thereof
A foamed rubber and Goodyear technology, applied in the field of preparation of the foamed rubber, can solve problems such as increasing the manufacturing cost of finished shoes, and achieve the effects of improving elasticity, low density and good technical requirements
- Summary
- Abstract
- Description
- Claims
- Application Information
AI Technical Summary
Problems solved by technology
Method used
Examples
Embodiment 1
[0019] Embodiment 1: the preparation method of double-density Goodyear outsole internal foam rubber, comprises the following steps:
[0020] a. Weigh 800kg of natural rubber, 500kg of styrene-butadiene rubber, 1100kg of reclaimed rubber, 50kg of active zinc oxide, 40kg of stearic acid, 20kg of anti-aging agent 4010NA, 700kg of N330 carbon black, 400kg of light calcium carbonate, 80kg of engine oil, 200kg of phenolic resin, S -8015kg, accelerator CZ35kg, foaming agent H10kg, urea 10kg;
[0021] b. Mix the natural rubber with styrene-butadiene rubber and reclaimed rubber after mastication, disperse evenly and place it for one day;
[0022] c. Put the rubber obtained in step b into the internal mixer, add carbon black, light calcium carbonate, and phenolic resin to press down the top bolt, lift the top bolt after 40 seconds, add active zinc oxide, stearic acid, and anti-aging agent 4010NA , Foaming agent H and engine oil, press down the top bolt, and discharge the material afte...
Embodiment 2
[0026] Embodiment 2: the preparation method of double-density Goodyear outsole internal foam rubber, comprises the following steps:
[0027] a. Weigh 850kg of natural rubber, 550kg of styrene-butadiene rubber, 1150kg of reclaimed rubber, 55kg of active zinc oxide, 45kg of stearic acid, 25kg of antioxidant 4010NA, 750kg of N330 carbon black, 450kg of light calcium carbonate, 90kg of engine oil, and phenolic resin 210kg, S-8016kg, accelerator CZ38kg, foaming agent H12kg, urea 12 kg;
[0028] b. Mix the natural rubber with styrene-butadiene rubber and reclaimed rubber after mastication, disperse evenly and place it for one day;
[0029] c. Put the rubber obtained in step b into the internal mixer, add carbon black, light calcium carbonate, and phenolic resin to press down the top bolt, lift the top bolt after 50 seconds, and add active zinc oxide, stearic acid, and anti-aging agent 4010NA , Foaming agent H and engine oil, press down the top bolt, and discharge the material afte...
Embodiment 3
[0033] Embodiment 3: the preparation method of double-density Goodyear outsole internal foam rubber, comprises the following steps:
[0034] a. Weigh 900kg of natural rubber, 600kg of styrene-butadiene rubber, 1200kg of reclaimed rubber, 60kg of active zinc oxide, 45kg of stearic acid, 25kg of antioxidant 4010NA, 750kg of N330 carbon black, 450kg of light calcium carbonate, 100kg of engine oil, 225kg of phenolic resin, S-8017kg, accelerator CZ40kg, foaming agent H15kg, urea 15kg;
[0035] b. Mix the natural rubber with styrene-butadiene rubber and reclaimed rubber after mastication, disperse evenly and place it for one day;
[0036] c. Put the rubber material obtained in step b into the internal mixer, add carbon black, light calcium carbonate, and phenolic resin to press down the top bolt, lift the top bolt after 75 seconds, add active zinc oxide, stearic acid, and anti-aging agent 4010NA , Foaming agent H and engine oil, press down the top bolt, and discharge the material ...
PUM
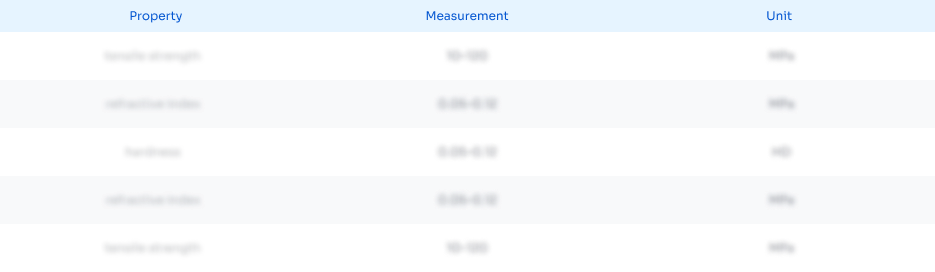
Abstract
Description
Claims
Application Information

- Generate Ideas
- Intellectual Property
- Life Sciences
- Materials
- Tech Scout
- Unparalleled Data Quality
- Higher Quality Content
- 60% Fewer Hallucinations
Browse by: Latest US Patents, China's latest patents, Technical Efficacy Thesaurus, Application Domain, Technology Topic, Popular Technical Reports.
© 2025 PatSnap. All rights reserved.Legal|Privacy policy|Modern Slavery Act Transparency Statement|Sitemap|About US| Contact US: help@patsnap.com