Hardness testing method and usage thereof
A detection method and hardness technology, applied in the direction of testing material hardness, etc., can solve the problems of test failure, crushing, failure to cover reinforcement, tough phase and matrix, etc.
- Summary
- Abstract
- Description
- Claims
- Application Information
AI Technical Summary
Problems solved by technology
Method used
Image
Examples
Embodiment 1
[0068] use image 3 , 4 The shown frustum-shaped detection indenter is used for the aluminum matrix composite material with the smallest volume fraction (27.7%) among the selected volume fractions. image 3 , 4 The end face is Ф6mm, Ф8mm, Ф10mm, Ф12mm conical) using the unique function of this system (the stress-strain curve test system of the load applied to the indenter and the displacement of the indenter), measured and displayed during the test (loading) process stress-strain curve. In this way, the indentation produced by the inspected sample under different indenter sizes is used to detect whether each component in the composite material is effectively covered (the minimum size of the indenter should be selected to determine the inspected material).
[0069] Figure 9 When using different sizes of conical indenters for the test, the stress diagram under different strains, it can be seen that the composite material corresponding to the above volume fraction (27.7%) ha...
Embodiment 2
[0072] use image 3 , 4 The frustum-shaped detection indenter shown in the figure is used for different volume fractions (27.7% 30.98% 40.2%) of aluminum matrix composites. We use this system to conduct indenter indentation depth and hardness test parameters, and choose the original planar indenter of this system ( The end face is Ф10mm conical—to ensure that the indentation area produced by the indenter of the hardness tester can cover the reinforcement, tough phase and matrix) using the unique function of this system (the stress-strain curve of the load applied to the indenter and the displacement of the indenter) test system), measure and display the stress-strain curve during the test (loading) as Figure 10 shown. In this way, it is used to detect whether any component of the tested sample is crushed (determine the crushed depth of the tested material).
[0073] And use a unique control method (depth control system) to control the indentation depth of the indenter ≯ th...
Embodiment 3
[0075] use image 3 , 4 The frustum-shaped detection indenter shown in the figure is used for aluminum, copper, and iron-based composite materials. We use this system to conduct hardness test parameters. Stress-strain curve test system of the applied load of the indenter and the displacement of the indenter), and the stress-strain curve is measured and displayed during the test (loading) as Figure 11 shown. In this way, it is used to detect whether any component of the tested sample is crushed (determine the crushed depth of the tested material). It can be seen that the composite materials of different matrices have different corresponding crushing depths, so different choices should be made in the hardness test.
[0076]
PUM
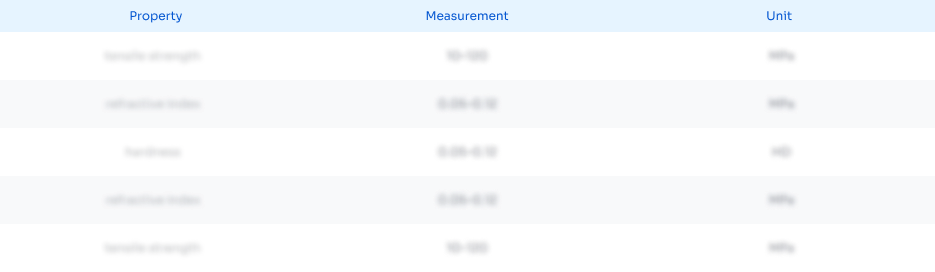
Abstract
Description
Claims
Application Information

- Generate Ideas
- Intellectual Property
- Life Sciences
- Materials
- Tech Scout
- Unparalleled Data Quality
- Higher Quality Content
- 60% Fewer Hallucinations
Browse by: Latest US Patents, China's latest patents, Technical Efficacy Thesaurus, Application Domain, Technology Topic, Popular Technical Reports.
© 2025 PatSnap. All rights reserved.Legal|Privacy policy|Modern Slavery Act Transparency Statement|Sitemap|About US| Contact US: help@patsnap.com